4130 metalworks
Mechanical
- Sep 22, 2024
- 3
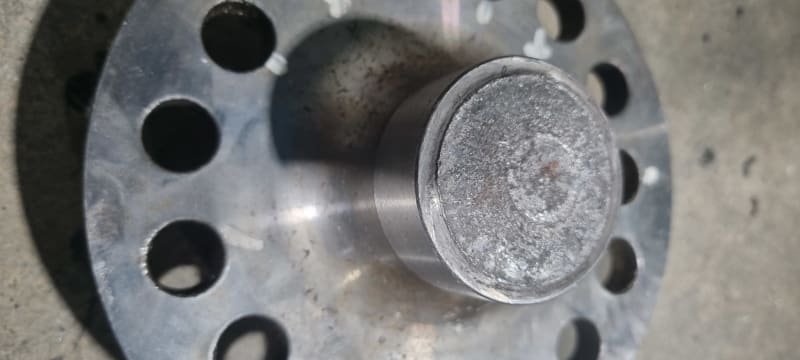
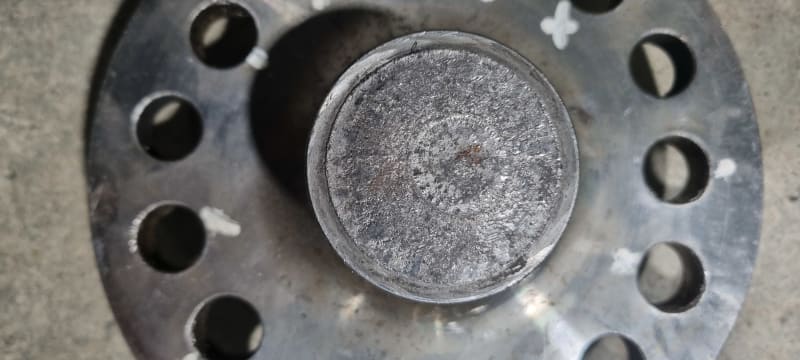
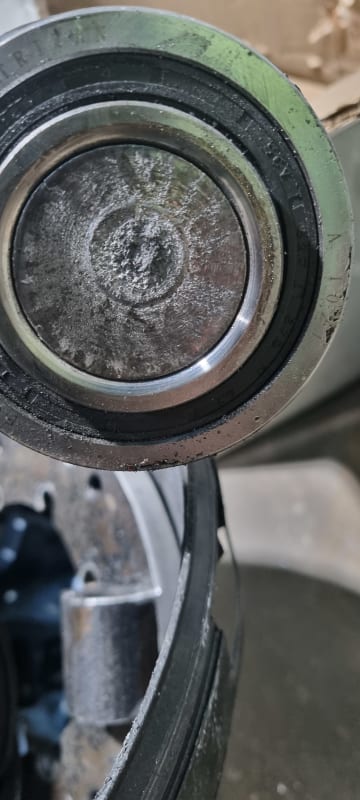
Hi, I'd like to get the groups thoughts on why this axle shaft failed and how to best go about testing the rest of them. The shaft is heat treated 4140, from machining the splines the hardness seems to be the outer 2-3mm.
Unfortunately I don't have much information from the manufacturer to go with
The vehicle is reasonably heavy but low powered and was travelling at speed when this happened
Thanks in advance for any help