Hi, I'm trying to wrap a polymer sheet (C3D8R elements) onto a wire (B31 elements) using a pressure applied to the sheet. The wire component is completely fixed. Currently I have general contact with a penalty applied to the entire model. The polymer sheet passes about 1/3rd of the way through the wire before it looks like it comes into contact. Does anyone have any suggestions on how I could change this so that polymer wraps around the outer edge of the beam element?
Thanks!
Thanks!
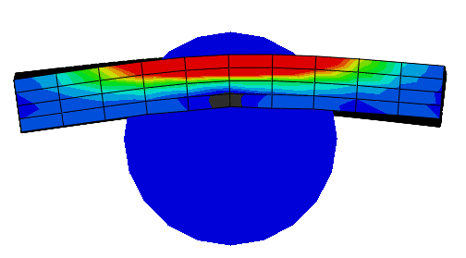