Hi there,
I am thinking through a steel beam-column detail that will be anchored to baseplates on both ends.
From a construction point of view, I am trying to visualise how I can get it to work.
Essentially if the contractor installs the post-installed anchor bolts on both sides there won't be enough space to fit/slide the beam in.
In situations like this, is the construction sequence as follows?
- Contractor marks anchor bolt locations on both sides
- Contractor installs the post-installed anchor bolts on one side only
- Steel beam with the base plate pre-welded is lifted into place
- With the steel beam in place, the contractor installs the post-installed anchor bolts on the other side (which would require injecting the epoxy through the baseplate hole and inserting the anchors through the base plate holes?)
Is this a fine approach or is there a better way to construct this or a detail that I should be considering to counteract this issue?
I built in about 4" of tolerance into the placement by including an allowance for 2" grout on either side, although this isn't enough tolerance to avoid clashing with the anchors.
The beam-column is subject to quite a high axial force.
I am thinking through a steel beam-column detail that will be anchored to baseplates on both ends.
From a construction point of view, I am trying to visualise how I can get it to work.
Essentially if the contractor installs the post-installed anchor bolts on both sides there won't be enough space to fit/slide the beam in.
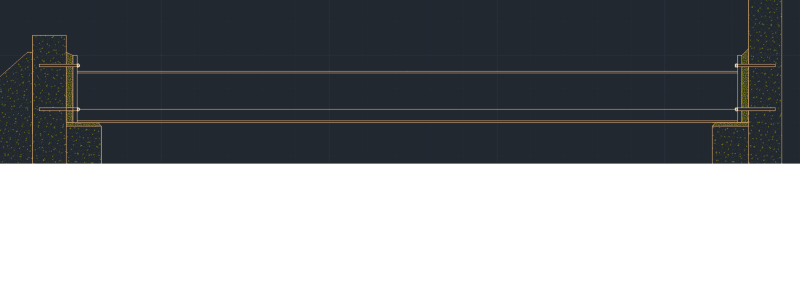
In situations like this, is the construction sequence as follows?
- Contractor marks anchor bolt locations on both sides
- Contractor installs the post-installed anchor bolts on one side only
- Steel beam with the base plate pre-welded is lifted into place
- With the steel beam in place, the contractor installs the post-installed anchor bolts on the other side (which would require injecting the epoxy through the baseplate hole and inserting the anchors through the base plate holes?)
Is this a fine approach or is there a better way to construct this or a detail that I should be considering to counteract this issue?
I built in about 4" of tolerance into the placement by including an allowance for 2" grout on either side, although this isn't enough tolerance to avoid clashing with the anchors.
The beam-column is subject to quite a high axial force.