michelemarchiol
Civil/Environmental
Dears,
I have a question regarding this kind of connection.
It's a welded connection between beams, as shown in the image uploaded.
Secondary beams have notches in both flanges. Secondary beams are welded to the principal beam in 3 points: (1) in bottom flange; (2) in the web; (3) in top flange
A designer proposed me to use this kind of joint, but to be honest I have never seen this kind of solution before and I don't really like it (due to the "holes" between secondary beam web and principal beam flanges).
Is this a solution that you have just seen before? Have you some reason to avoid this kind of solution?
Please tell me what you think about this joint.
¯
Thank you in advance.
I have a question regarding this kind of connection.
It's a welded connection between beams, as shown in the image uploaded.
Secondary beams have notches in both flanges. Secondary beams are welded to the principal beam in 3 points: (1) in bottom flange; (2) in the web; (3) in top flange
A designer proposed me to use this kind of joint, but to be honest I have never seen this kind of solution before and I don't really like it (due to the "holes" between secondary beam web and principal beam flanges).
Is this a solution that you have just seen before? Have you some reason to avoid this kind of solution?
Please tell me what you think about this joint.
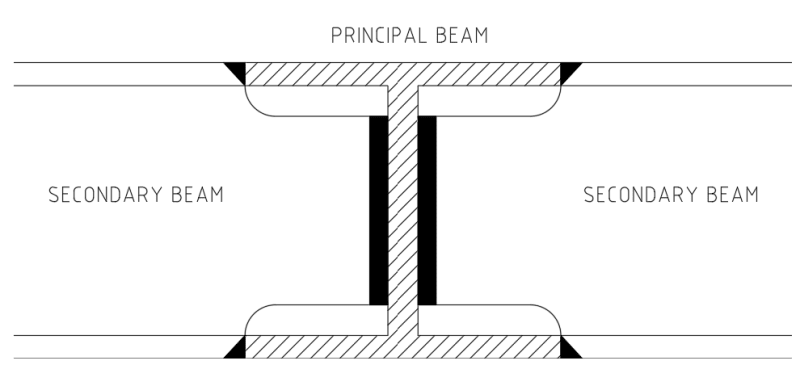
Thank you in advance.