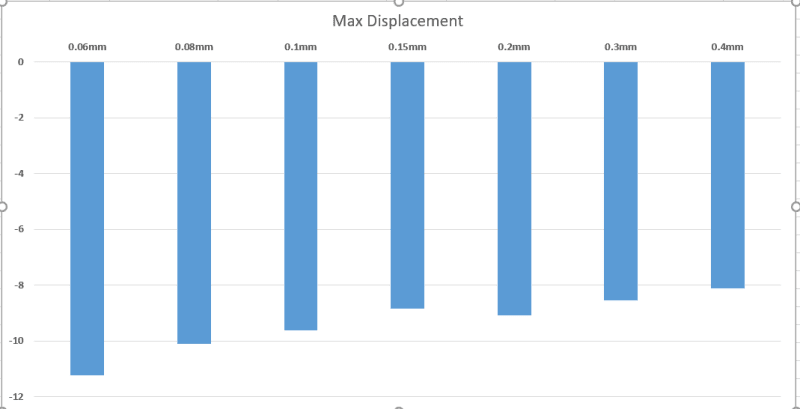
In the sandwich composite plate comprised of ceramic, honeycomb and composite layup sequence, the variation of honeycomb thickness is done and rest all the parameters as same. For the same blast load and same boundary condition, there is a sudden behavioural change for the thickness of 0.15mm. Modelling the honeycomb layer and composite layer as shell and ceramic as solid. Can anyone able to explain this sudden behavioural change. I redo the simulation for more than 2 times and got the same graph.