mte12
Structural
- Mar 1, 2022
- 141
It looks like welding aluminum decreases strength in weld/heat affected zones.
As an alternative, I was thinking of bending a single sheet and cutting voids (in order to reduce weight).
Bending sheet seems like it would cold work the material, hence assuming no loss of strength at least. Would this assumption be correct?
Also is radii shown in table below achievable for arrangement shown. Currently looking at 6mm or 8mm Grade 5083.
[URL unfurl="true"]https://www.australwright.com.au/wp-content/uploads/2019/02/Aluminium_Catalogue.pdf[/url]
As an alternative, I was thinking of bending a single sheet and cutting voids (in order to reduce weight).
Bending sheet seems like it would cold work the material, hence assuming no loss of strength at least. Would this assumption be correct?
Also is radii shown in table below achievable for arrangement shown. Currently looking at 6mm or 8mm Grade 5083.
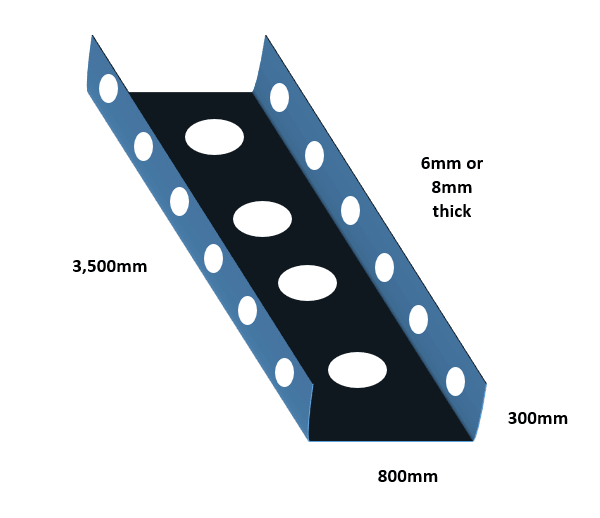
[URL unfurl="true"]https://www.australwright.com.au/wp-content/uploads/2019/02/Aluminium_Catalogue.pdf[/url]
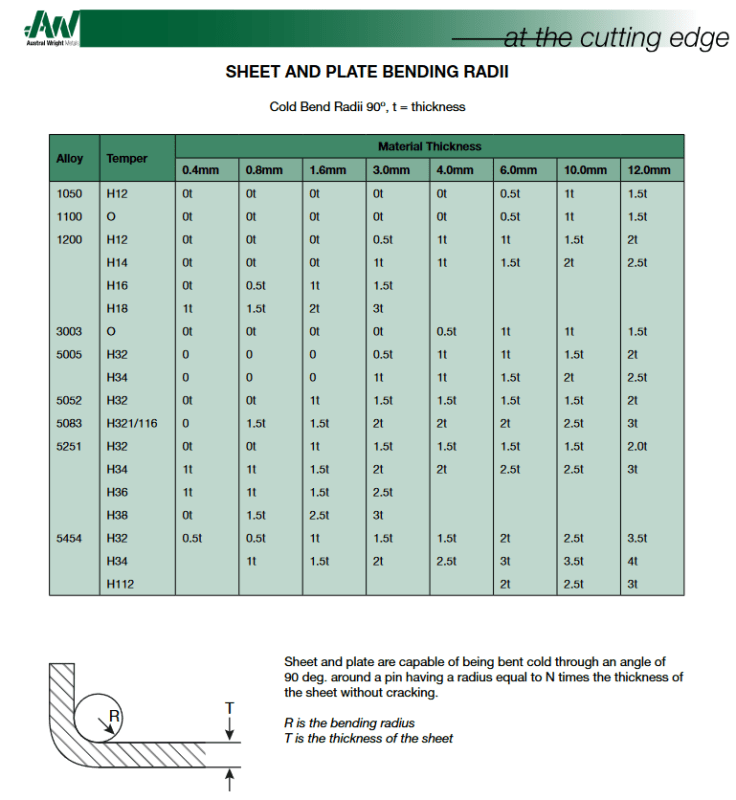