Tomfh
Structural
- Feb 27, 2005
- 3,485
What is your preferred detail for pinning a steel rafter to a concrete panel?
Here are some details I grabbed from the web, to aid discussion.
Some considerations:
A. Cast in weld plates vs. anchors?
B. Flexibility requirements? How to assess the anchor tension?
C. Seat vs web support?
D. Detail at joints vs Detail clear of joints?
E. Consideration of rafter size on connection choice?
Here are some details I grabbed from the web, to aid discussion.
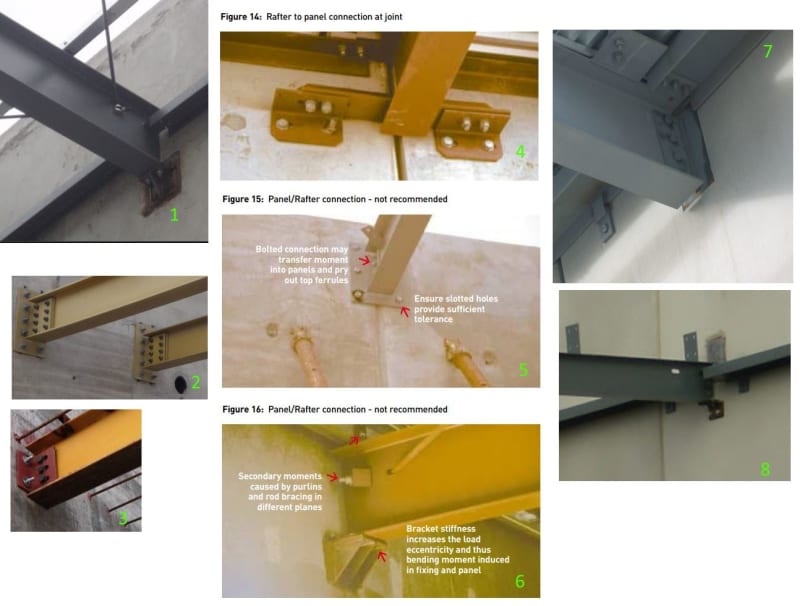
Some considerations:
A. Cast in weld plates vs. anchors?
B. Flexibility requirements? How to assess the anchor tension?
C. Seat vs web support?
D. Detail at joints vs Detail clear of joints?
E. Consideration of rafter size on connection choice?