jimmyjoeyphilp
Industrial
Interference fit? Industrial glues? Other methods?
Somewhat unusual situation. Let's say the magnet-rings have a diameter of 75 mm and a vertical and horizontal thickness of 2 mm. These magnet rings will be brought together in a handheld fashion on a regular basis and it would be unconscionable if they came loose or fell out. I'm wondering the best way to keep them in place.
The female "shell" each magnet will fit into could be (depending on model type) stainless steel, aluminum, brass or copper.
Here's an example of a "shell" half:
One half magnetic N pole, other half magnetic S pole.
Somewhat unusual situation. Let's say the magnet-rings have a diameter of 75 mm and a vertical and horizontal thickness of 2 mm. These magnet rings will be brought together in a handheld fashion on a regular basis and it would be unconscionable if they came loose or fell out. I'm wondering the best way to keep them in place.
The female "shell" each magnet will fit into could be (depending on model type) stainless steel, aluminum, brass or copper.
Here's an example of a "shell" half:
One half magnetic N pole, other half magnetic S pole.
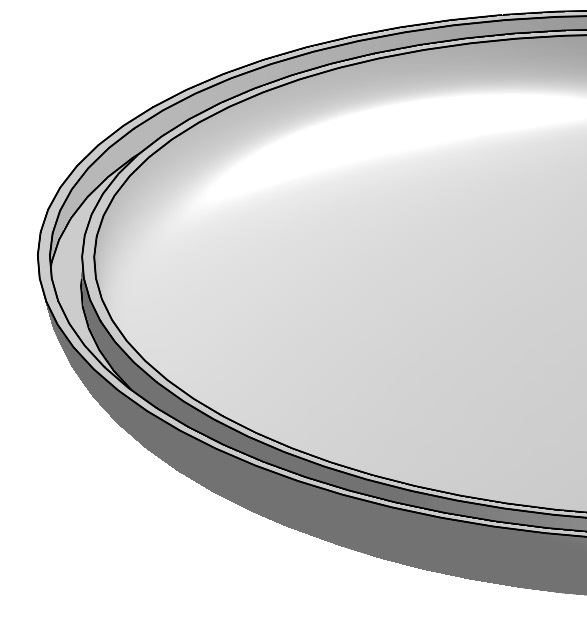