BR_mechanical_engineer
Mechanical
Hey guys! I hope you're doing well!
I need to build a device that makes a circular cut in a single hit on a steel plate, using a pneumatic cylinder. For this, I need to estimate the force that the cylinder needs to make the cut, as shown below.
The diameter to be cut is around 100 mm.
The compressed air line pressure is 6 bar.
The thickness of the AISI 1020 to be cut is 0.5 mm.
What intrigues me in this case is how to consider the contact area between the blade and the plate, since I intend to manufacture something like the image below.
Why do I want to use this geometry? I strongly believe that the cutting force vs cost ratio is more advantageous, precisely because of the area.
My plan is to estimate the shear force, and then with the air pressure used in the cylinder find a cross-sectional area to select the proper cylinder, assuming a 15% "safety factor" for the cylinder.
Are there any tips or tricks for considering the area of this slide and find an analytical solution?
Thanks in advance for the support, guys!
I need to build a device that makes a circular cut in a single hit on a steel plate, using a pneumatic cylinder. For this, I need to estimate the force that the cylinder needs to make the cut, as shown below.
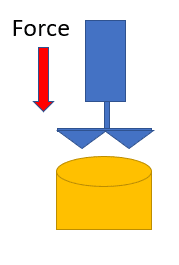
The diameter to be cut is around 100 mm.
The compressed air line pressure is 6 bar.
The thickness of the AISI 1020 to be cut is 0.5 mm.
What intrigues me in this case is how to consider the contact area between the blade and the plate, since I intend to manufacture something like the image below.
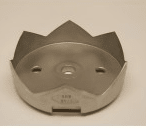
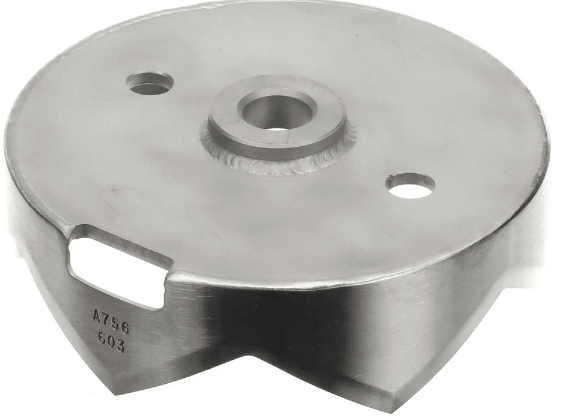
Why do I want to use this geometry? I strongly believe that the cutting force vs cost ratio is more advantageous, precisely because of the area.
My plan is to estimate the shear force, and then with the air pressure used in the cylinder find a cross-sectional area to select the proper cylinder, assuming a 15% "safety factor" for the cylinder.
Are there any tips or tricks for considering the area of this slide and find an analytical solution?
Thanks in advance for the support, guys!