Hi, the company I work for recently purchased a hot water boiler. Water flows through formed metal tubes while a burner provides heat.
The boiler installer filled it with water, performed a pressure test, and identified a leak before turning on the burner or main pump. One of the tubes has a crack around a flange. I don’t know how the flanges are formed but I have included pictures of a new tube end. The end is tapered and has a flange that is used to install the tubes. The tapered end is driven into a hole in the header of the boiler. Then a plate is bolted down and presses on the flange. I am told that this plate is only a mandated safety measure. Driving the tapered tube into the hole is sufficient to form a pressure-tight seal. I don't know the force of the plate on the flange.
The boiler company claims they pressure tested the boiler to 240 psi. We only tried to pressure test to 40 psi, but couldn’t achieve that pressure due to the leak.
The tube material as written on the tubes is “WEBCO A/SA 178-A/214 ERW 1.500 OD X .095 MW HT# GC77119”
Here is the Webco and ASTM specification:
Here is a video of the boiler manufacturer’s tube installation process:
There are indentations on the flange of every tube, presumably from the installation tool.
What do you think caused the crack? Obviously this is a highly stressed area due to the forming of the flange and the hammering during installation. Why would a crack develop spontaneously when no pressure is inside the tube? (i.e. I’m assuming the crack developed during shipping) I’m interested to hear your thoughts. Thanks!
New tube end
New tube end
New tube end
New tube end
New tube end
Wide angle of cracked tube in boiler (cracked tube circled in red)
Leaking tube
Crack
Crack
The boiler installer filled it with water, performed a pressure test, and identified a leak before turning on the burner or main pump. One of the tubes has a crack around a flange. I don’t know how the flanges are formed but I have included pictures of a new tube end. The end is tapered and has a flange that is used to install the tubes. The tapered end is driven into a hole in the header of the boiler. Then a plate is bolted down and presses on the flange. I am told that this plate is only a mandated safety measure. Driving the tapered tube into the hole is sufficient to form a pressure-tight seal. I don't know the force of the plate on the flange.
The boiler company claims they pressure tested the boiler to 240 psi. We only tried to pressure test to 40 psi, but couldn’t achieve that pressure due to the leak.
The tube material as written on the tubes is “WEBCO A/SA 178-A/214 ERW 1.500 OD X .095 MW HT# GC77119”
Here is the Webco and ASTM specification:
Here is a video of the boiler manufacturer’s tube installation process:
There are indentations on the flange of every tube, presumably from the installation tool.
What do you think caused the crack? Obviously this is a highly stressed area due to the forming of the flange and the hammering during installation. Why would a crack develop spontaneously when no pressure is inside the tube? (i.e. I’m assuming the crack developed during shipping) I’m interested to hear your thoughts. Thanks!
New tube end
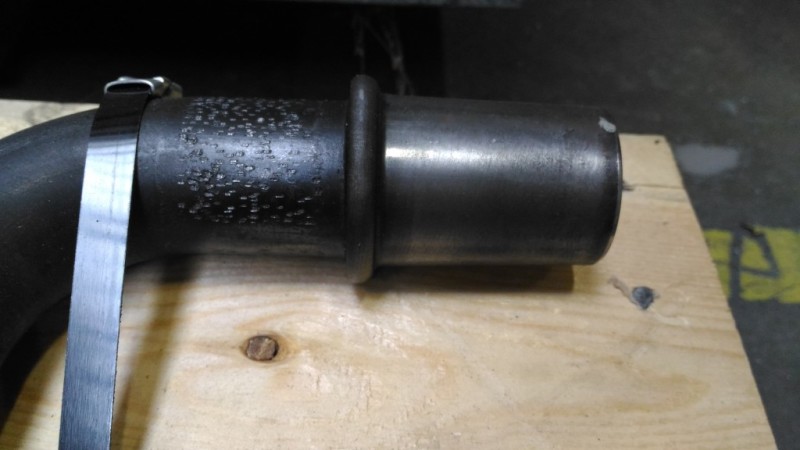
New tube end
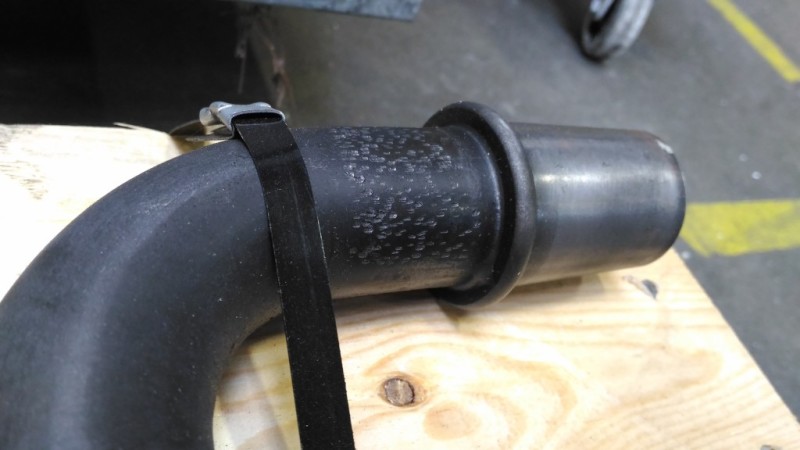
New tube end
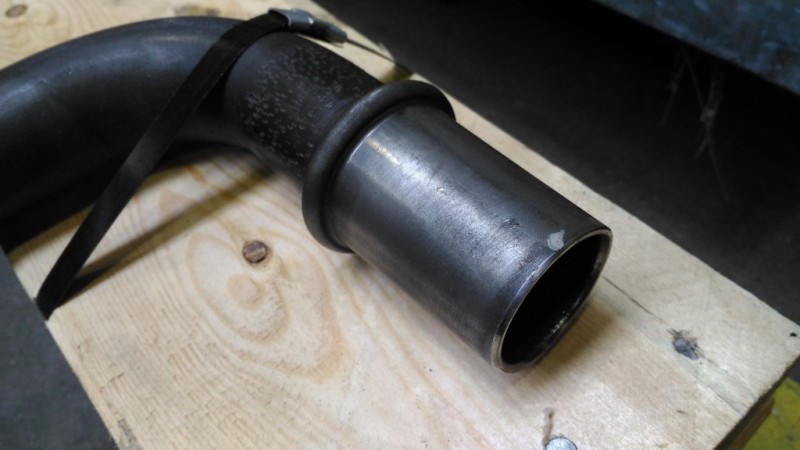
New tube end
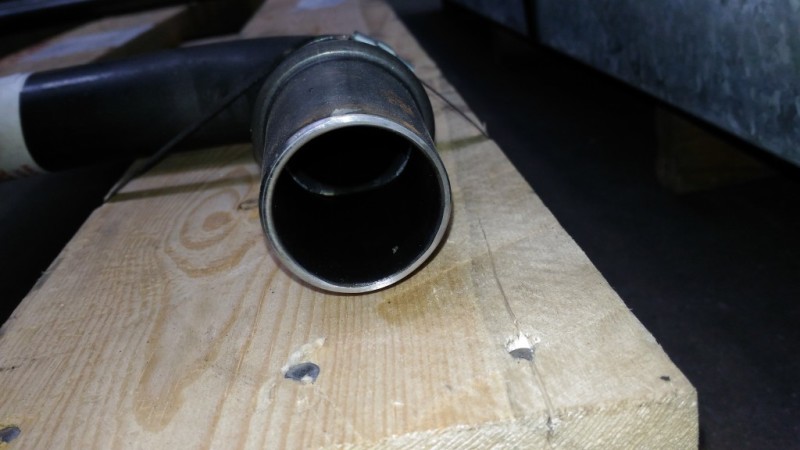
New tube end
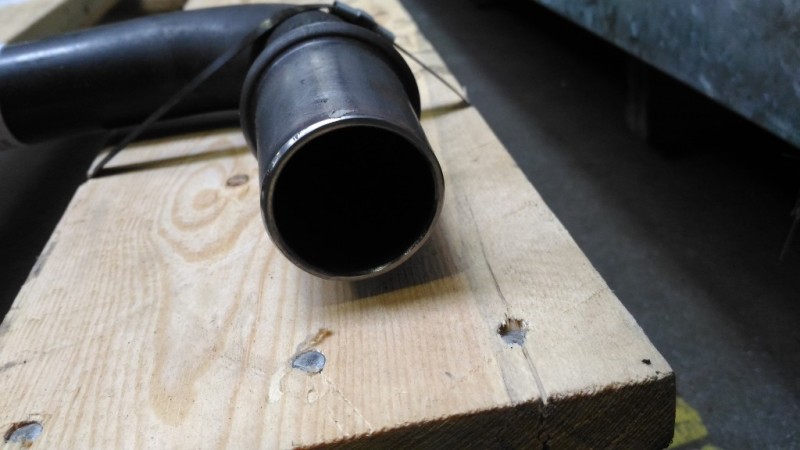
Wide angle of cracked tube in boiler (cracked tube circled in red)
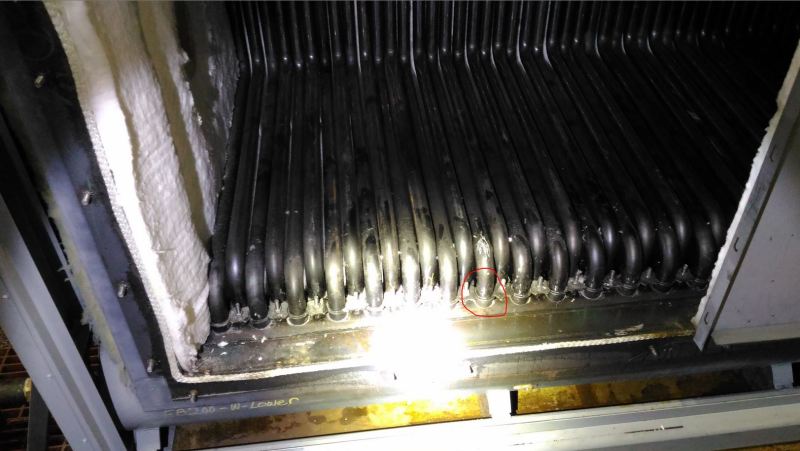
Leaking tube
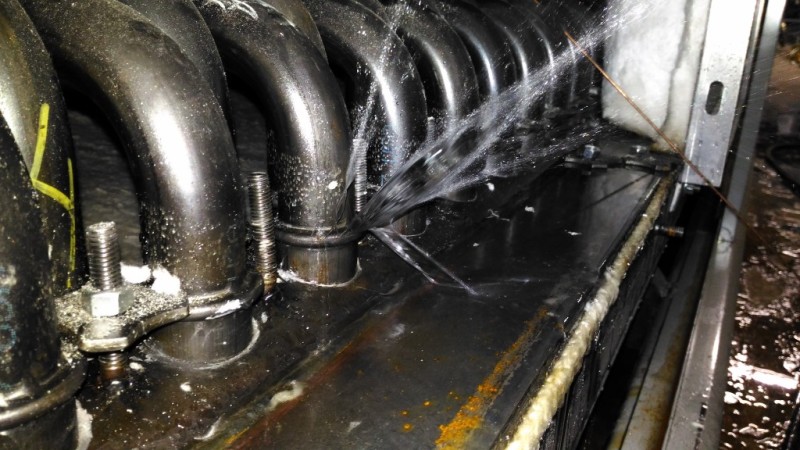
Crack
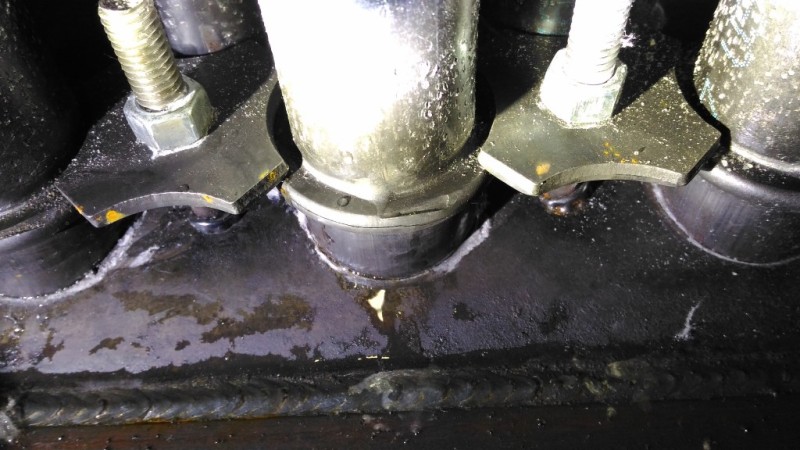
Crack
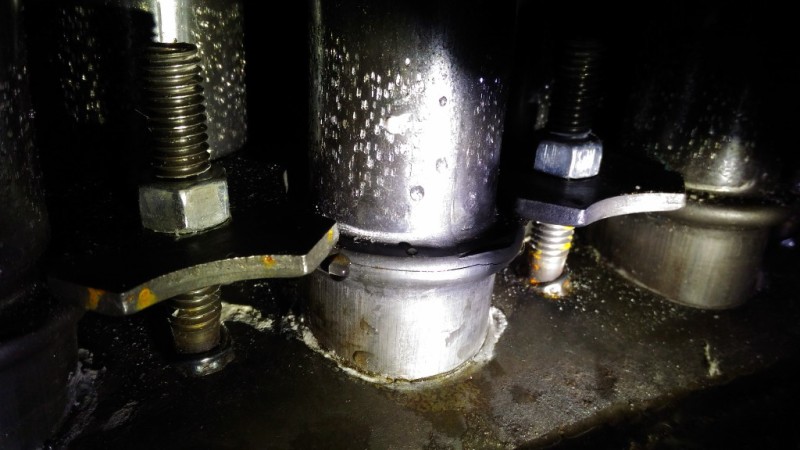