NeelArmstrong
Mechanical
Hello,
I have a composite laminate (modeled as an 18-part stack of 3d plates attached to one another via surface-to-surface ties) and separate part, all of which have connector holes (through which they are bolt-attached). I would like to use the abaqus fastener/connector capabilities to achieve the connection (rather than modeling the bolts). I have seen many examples of attaching shell components to one another, but not 3 or more solid parts. I have been trying a small-scale model (see image below) to figure how to do it but I have been having trouble.
What Ive tried so far (extending an example ive seen for a shell-to-shell case): I created 1 reference point for each plate in the small-scale model (the top center of each hole), coupled the points to the corresponding circumferential surfaces (surfaces that would be in contact with the bolt shaft, attached the points via wires, and applied cartesian+align section properties to the wires. Unfortunately, the exited with convergence issues.
Does anyone have experience with this or any tips they could offer? help would be greatly appreciated.
I have a composite laminate (modeled as an 18-part stack of 3d plates attached to one another via surface-to-surface ties) and separate part, all of which have connector holes (through which they are bolt-attached). I would like to use the abaqus fastener/connector capabilities to achieve the connection (rather than modeling the bolts). I have seen many examples of attaching shell components to one another, but not 3 or more solid parts. I have been trying a small-scale model (see image below) to figure how to do it but I have been having trouble.
What Ive tried so far (extending an example ive seen for a shell-to-shell case): I created 1 reference point for each plate in the small-scale model (the top center of each hole), coupled the points to the corresponding circumferential surfaces (surfaces that would be in contact with the bolt shaft, attached the points via wires, and applied cartesian+align section properties to the wires. Unfortunately, the exited with convergence issues.
Does anyone have experience with this or any tips they could offer? help would be greatly appreciated.
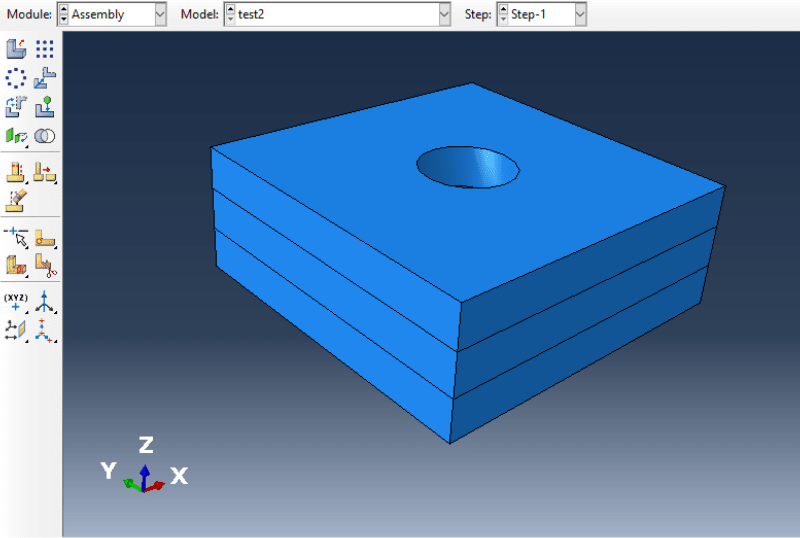