Hello all,
i need some guidance on solving a numerical problem, we are currently doing packing compression test as per API 622, picture attached below of sketch of test setup fixture.
as u can see in picture, packing is compressed by tightening bolt & nut which is putting force on spring through washer .
if i have given compressive stress value on packing (let's say 30 MPa) which we need to apply through washer by tightening bolt, can u tell me how to calculate tightening force which we need to apply on the nut and
and
how much turns should we rotate the nut to fully tighten the bolt with stress value shown above.
i need some guidance on solving a numerical problem, we are currently doing packing compression test as per API 622, picture attached below of sketch of test setup fixture.
as u can see in picture, packing is compressed by tightening bolt & nut which is putting force on spring through washer .
if i have given compressive stress value on packing (let's say 30 MPa) which we need to apply through washer by tightening bolt, can u tell me how to calculate tightening force which we need to apply on the nut and
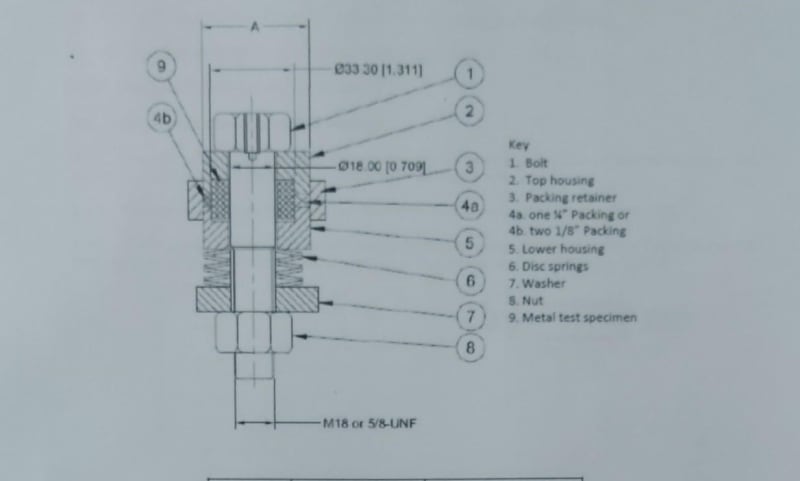
how much turns should we rotate the nut to fully tighten the bolt with stress value shown above.