Hi there,
could someone provide some general guidance on how to bolt together multiple hollow sections? I am using only rectangular sections.
Also, I attached the figure below and am interested in which of the two ways is the "correct" one, when it comes to connecting two rectangular sections side by side.
Many thanks,
Uroš
could someone provide some general guidance on how to bolt together multiple hollow sections? I am using only rectangular sections.
Also, I attached the figure below and am interested in which of the two ways is the "correct" one, when it comes to connecting two rectangular sections side by side.
Many thanks,
Uroš
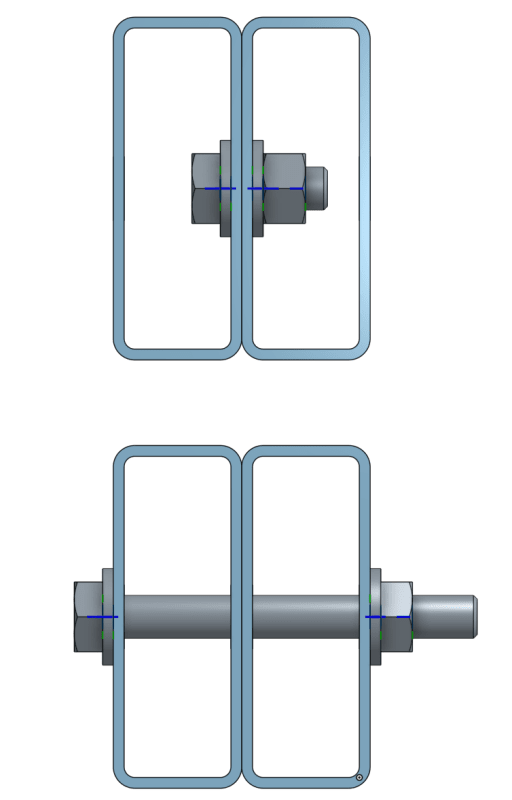