Pulsater555
Petroleum
Hello All,
I am currently looking at an application where we want to boost an engine to provide more horse power to a compressor. The engine type would either be a Waukesha or a CAT natural gas engine for compression applications, exp: 7044GSI or 3512. This application would only be used when the compressor frame can take more horse power than what the engine can normally provide.
The waste heat recovery system will be able to provide an additional 100hp. The idea is to tie the motor to the cooler jack shaft and feed the power back into the engine thus providing more power for the compressor to utilize.
What are the communities thoughts on a configuration like this? Has a system like this been tried before?
We are imagining that a system like this would be similar to an electrically assisted bicycle in the sense that the electric motor can kick in to help the bicycler while peddling.
I am currently looking at an application where we want to boost an engine to provide more horse power to a compressor. The engine type would either be a Waukesha or a CAT natural gas engine for compression applications, exp: 7044GSI or 3512. This application would only be used when the compressor frame can take more horse power than what the engine can normally provide.
The waste heat recovery system will be able to provide an additional 100hp. The idea is to tie the motor to the cooler jack shaft and feed the power back into the engine thus providing more power for the compressor to utilize.
What are the communities thoughts on a configuration like this? Has a system like this been tried before?
We are imagining that a system like this would be similar to an electrically assisted bicycle in the sense that the electric motor can kick in to help the bicycler while peddling.
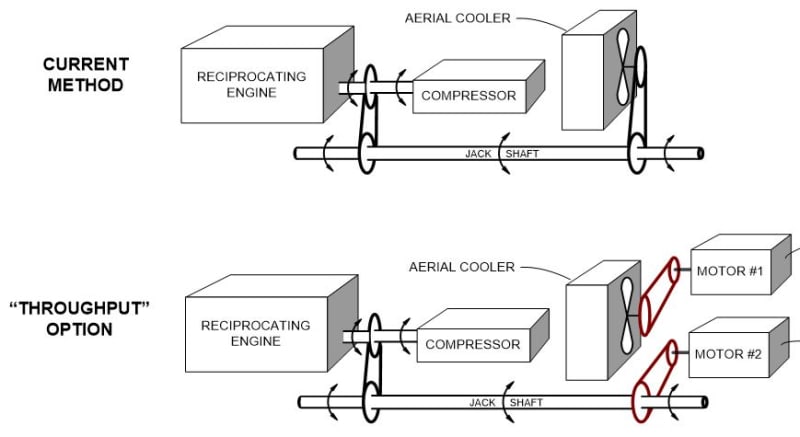