I tried to use Abaqus for external turning simulation, set the workpiece speed to 6.28/s, and set the analysis step time to 1. Theoretically, the workpiece should rotate one revolution, but the output shows that the workpiece reference point did rotate one revolution, but the rotation involved in cutting seems to be only a small rotation.
1. the f0llowing figure shows my boundary conditions set for the workpiece(The workpiece reference point is coupled to the left cross-section.).
2. And the following figure shows the rotation angle of the reference point on the workpiece.
3. The cloud diagram below shows how little the workpiece actually turns.
I would like to know why the actual rotation angle of the workpiece does not match what I set, and how I can set it so that they match. Thank you very much!
1. the f0llowing figure shows my boundary conditions set for the workpiece(The workpiece reference point is coupled to the left cross-section.).
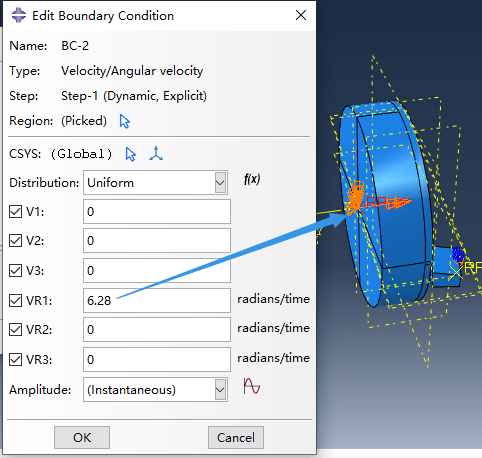
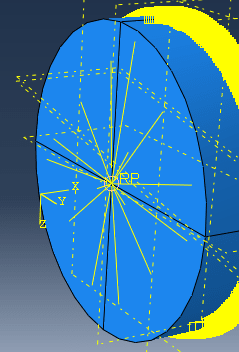
2. And the following figure shows the rotation angle of the reference point on the workpiece.
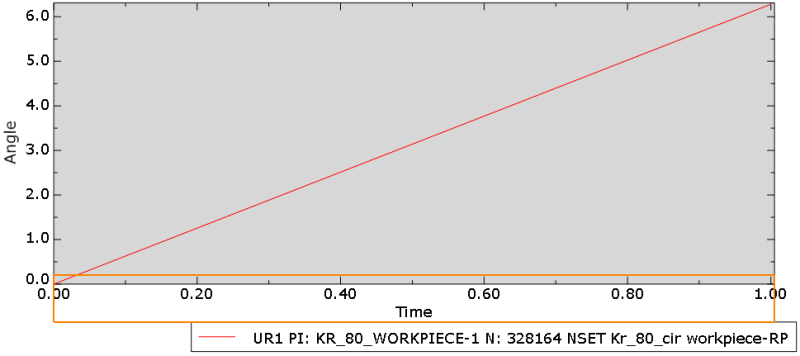
3. The cloud diagram below shows how little the workpiece actually turns.
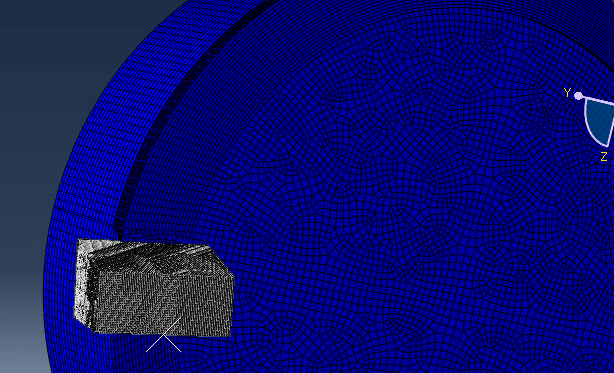
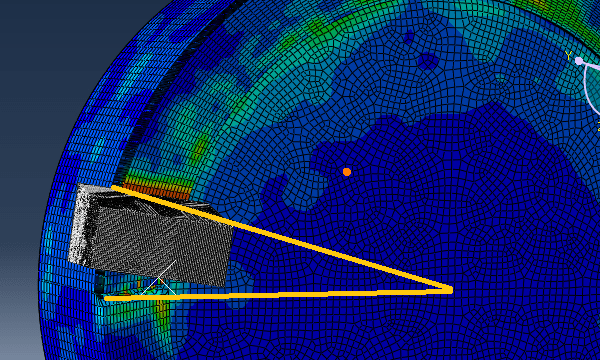
I would like to know why the actual rotation angle of the workpiece does not match what I set, and how I can set it so that they match. Thank you very much!