Nitesh Sadashiva
Civil/Environmental
- Jan 9, 2020
- 33
Hello,
In one of the project for which I am doing connection engineering, there was a brace with Clevis detail at the end connection as shown in the below sketch.
The specified design force was 20 kips. After discussion with the fabricator, We changed the connection to use end plate and two fork plates as shown in the below sketch.
In approval return of shop drawing, EOR has commented as shown in below sketch. I am not understanding the EOR comment. Can anyone help me on this?
In one of the project for which I am doing connection engineering, there was a brace with Clevis detail at the end connection as shown in the below sketch.
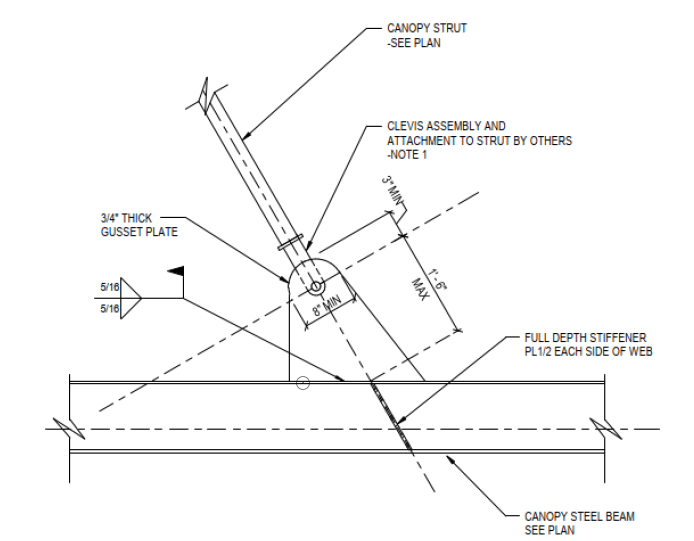
The specified design force was 20 kips. After discussion with the fabricator, We changed the connection to use end plate and two fork plates as shown in the below sketch.
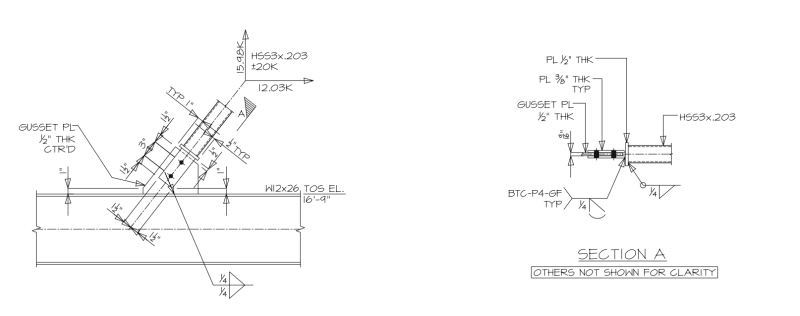
In approval return of shop drawing, EOR has commented as shown in below sketch. I am not understanding the EOR comment. Can anyone help me on this?
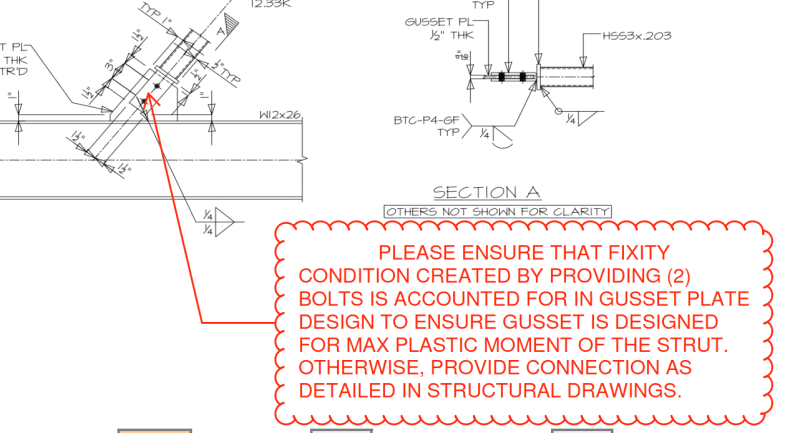