bddp9
Mechanical
- Feb 17, 2024
- 5
Hello,
I've been working on a drone project and need some help with a mechanism for closing and expanding the drone's arms. Please see image below. What are some alternatives? Right now in my model i have a small servo motor and gears that can open the arms. Any alternatives? The OD is 45mm. The top half will be for batteries and the bottom will be for anything electrical or mechanical.
I've been working on a drone project and need some help with a mechanism for closing and expanding the drone's arms. Please see image below. What are some alternatives? Right now in my model i have a small servo motor and gears that can open the arms. Any alternatives? The OD is 45mm. The top half will be for batteries and the bottom will be for anything electrical or mechanical.
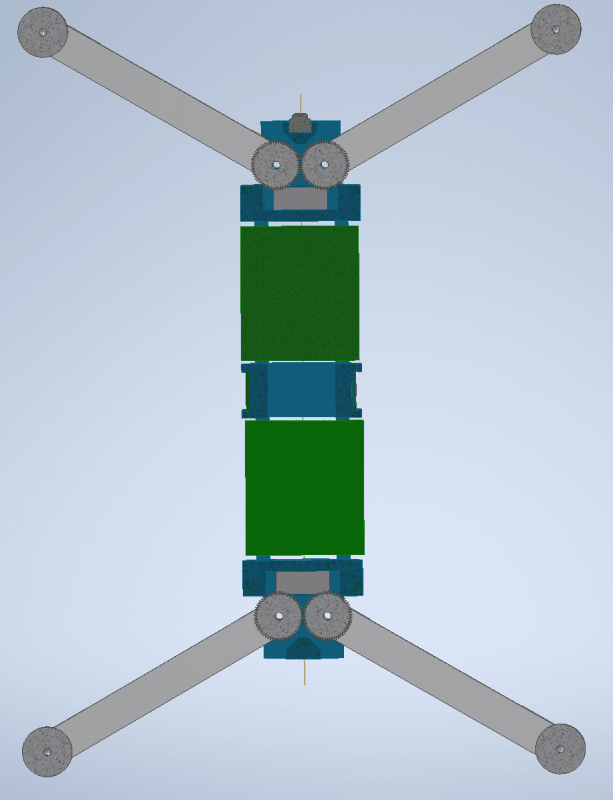
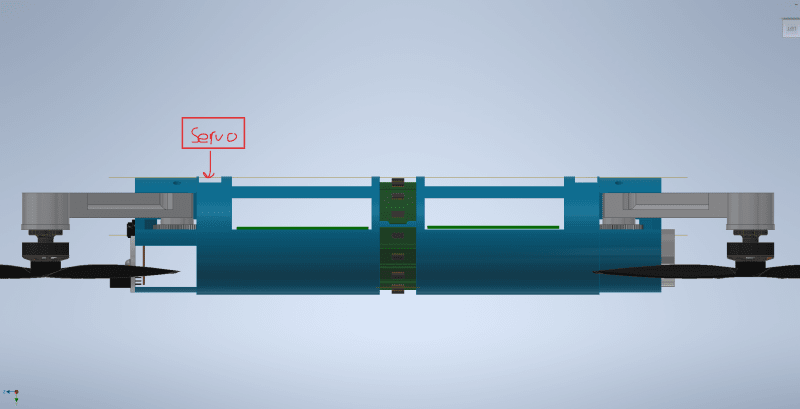