Hey guys
We had this screw drive shaft break at the welds today. It was installed less than a year ago and I’d estimate only 1500 hours on it.
Just curious what you guys think on the failure. The drawings do state the plate can be welded to the shaft to develop full strength. I wonder if this means the shaft should have been welded with a much bigger weld?
Anyhow just wanted to see what you guys think
Thanks!
We had this screw drive shaft break at the welds today. It was installed less than a year ago and I’d estimate only 1500 hours on it.
Just curious what you guys think on the failure. The drawings do state the plate can be welded to the shaft to develop full strength. I wonder if this means the shaft should have been welded with a much bigger weld?
Anyhow just wanted to see what you guys think
Thanks!
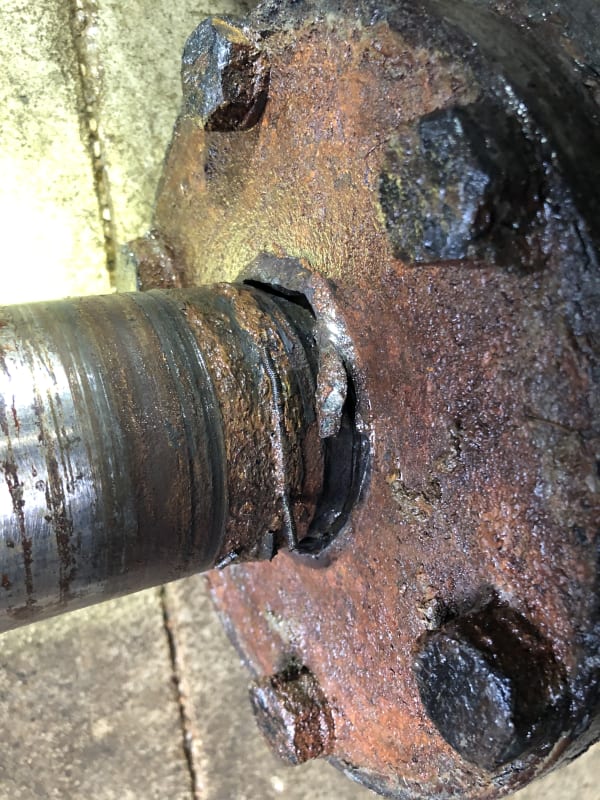
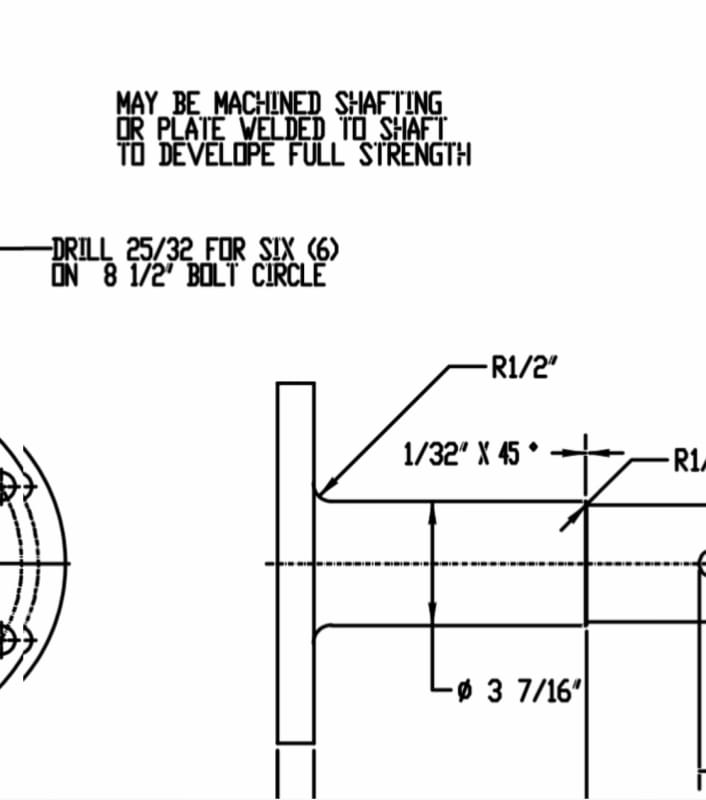
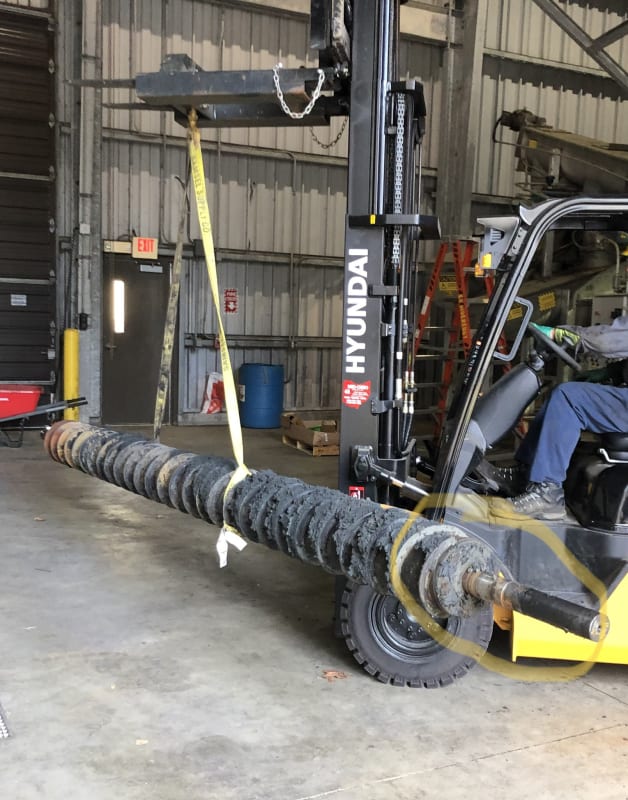
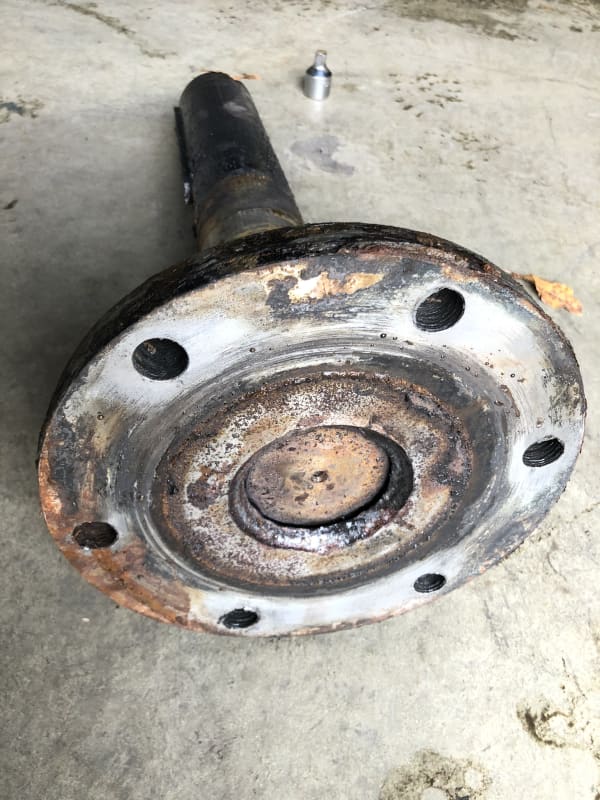
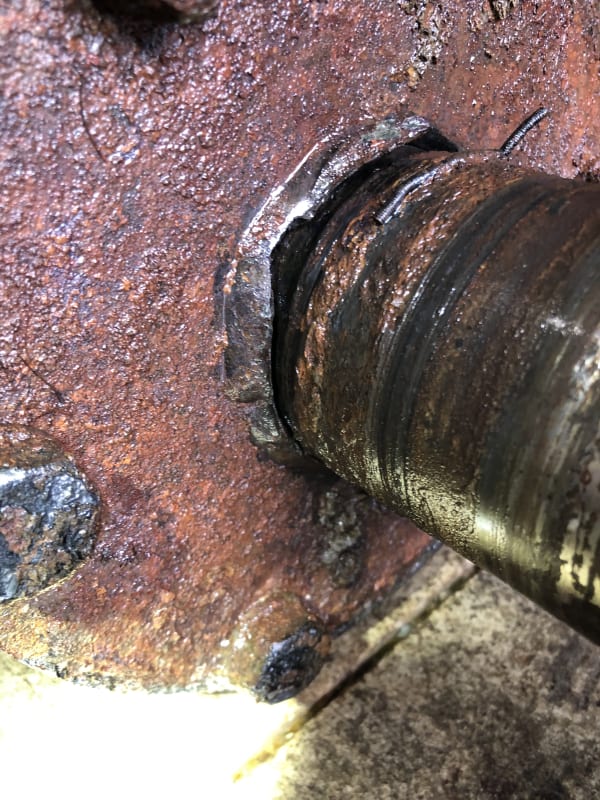