Anatoly_k
Mechanical
- Apr 21, 2022
- 10
Dear all,
I am learning Ansys and trying to estimate pipe burst pressure with FEA. I use nonlinear material as per ASME VII-2 part 5, however my solution does not stop when failure has happened. On the picture it is seen that thee pipe wall is open but I had to interrupt the solver due to endless process.
Also somehow the opening happens on one side only, despite I would expect some symmetry, what is the possible the reason?
I would also want to know how to "replace "nodes distortion with their disintegration to obtain more realistic result?
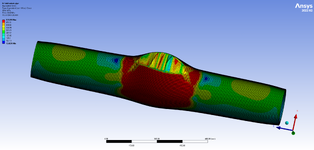
I am learning Ansys and trying to estimate pipe burst pressure with FEA. I use nonlinear material as per ASME VII-2 part 5, however my solution does not stop when failure has happened. On the picture it is seen that thee pipe wall is open but I had to interrupt the solver due to endless process.
Also somehow the opening happens on one side only, despite I would expect some symmetry, what is the possible the reason?
I would also want to know how to "replace "nodes distortion with their disintegration to obtain more realistic result?
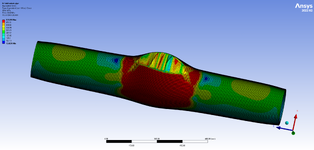