keith olsen
Marine/Ocean
- Aug 31, 2016
- 2
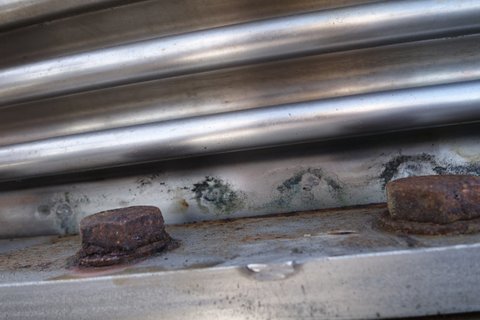
Good Day - First timer here hoping to get some good opinions
A portion of failed bellows is shown in photo. This is a 1.7 M diameter bellow recently installed on the outlet of a marine exhaust gas scrubber. In a few short months it has developed holes along lower portion of installation very close to bolting. Although some in our organization suspect the inner sleeve is retaining sour water (partially acidic) my thinking is it appears to be pitting corrosion due to surface damage when bolts are being knocked up tight. It is in a marine atmosphere. After the pitting starts the wrong bolting sets up local galvanic cell further accelerating problem. Bellow material is 1.4662 flanges 1.4541. Any thoughts most welcome!
Keith