Hello all,
I'm having some trouble with a C-hook for aluminum coils
My customer asked to verify the SWL of the hook. He made it using S355JR (510 MPa rupture, 355 MPa yield).
I tried to verify it using FEM method (PTC Simulate) and applying EN13155 rules: at 2xSWL + weight the maximum equivalent stress should be less then the yield strenght.
Well, my calculation says that the maximum stress is at about 600 MPa!!
So I tried to verify another certified hook, and the stresses are about the same. So, my doubt is: is the material not equivalent? Which materials are generally used in C-hook construction? S690 maybe?
TIA,
Max
attach: tensions over blue are over yield strenght (335 depending by thickness).
I'm having some trouble with a C-hook for aluminum coils
My customer asked to verify the SWL of the hook. He made it using S355JR (510 MPa rupture, 355 MPa yield).
I tried to verify it using FEM method (PTC Simulate) and applying EN13155 rules: at 2xSWL + weight the maximum equivalent stress should be less then the yield strenght.
Well, my calculation says that the maximum stress is at about 600 MPa!!
So I tried to verify another certified hook, and the stresses are about the same. So, my doubt is: is the material not equivalent? Which materials are generally used in C-hook construction? S690 maybe?
TIA,
Max
attach: tensions over blue are over yield strenght (335 depending by thickness).
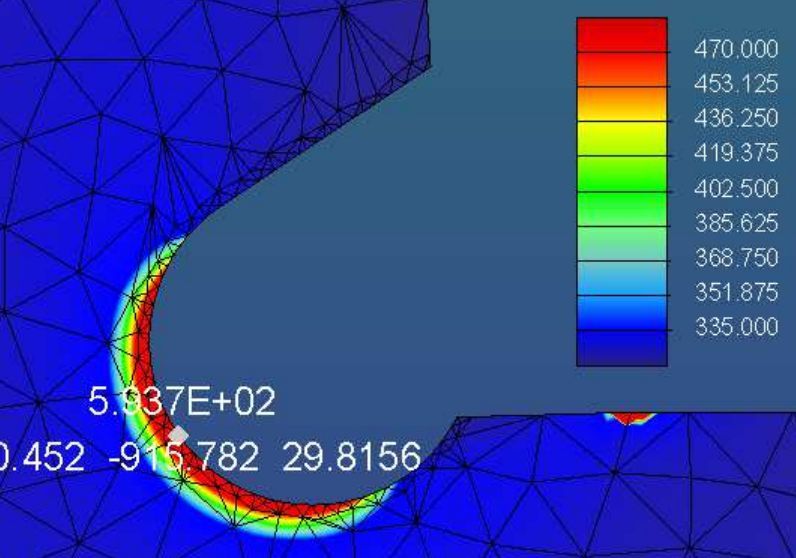