Hayesmc
Civil/Environmental
- Jun 26, 2019
- 3
On a project I worked on, a section of 12" C900 fire line completely burst while undergoing a pressure test. The attached image shows the length of pipe that blew up between two 45 degree elbows. Due to changes during construction, a high point existed at the elbow on the right, without an air release, and likely had an air bubble. As the tester introduced pressure to test the fire line (his goal was to test the fire line at 200 psi for 2 hours), the pipe section blew up at about 180 psi. Fortunately, no one was hurt. The tester said the air pressure at the high point was likely 500-600 psi and caused the explosion. Its also worth noting the section between the elbows was the last section to be installed - so its likely the contractor had to push and pull the pipe to make sure the connections could be made between the elbows. This likely introduced some extra stresses to the C900 pipe at the elbows. It also noteworthy that this section of pipe was left exposed during testing.
Does anyone have any experience with such an incident?
It seems prudent that as the fire line was pressurized, the volume of the air bubble decreased and increased air pressure. If the tester measure 180 psi water pressure, how could one calculate the air pressure at the air bubble?
It is common in our area to not draw up a profile for fire lines; therefore it would seem likely that high points and air pockets would existing in other fire lines and other bursting incidents would have happened - but they don't. This makes me consider the pre-loaded stresses in the pipe in order to match the elbows and whether this particular section of pipe material could have been substandard.
Any feedback or experience in this matter is really appreciated.
Does anyone have any experience with such an incident?
It seems prudent that as the fire line was pressurized, the volume of the air bubble decreased and increased air pressure. If the tester measure 180 psi water pressure, how could one calculate the air pressure at the air bubble?
It is common in our area to not draw up a profile for fire lines; therefore it would seem likely that high points and air pockets would existing in other fire lines and other bursting incidents would have happened - but they don't. This makes me consider the pre-loaded stresses in the pipe in order to match the elbows and whether this particular section of pipe material could have been substandard.
Any feedback or experience in this matter is really appreciated.
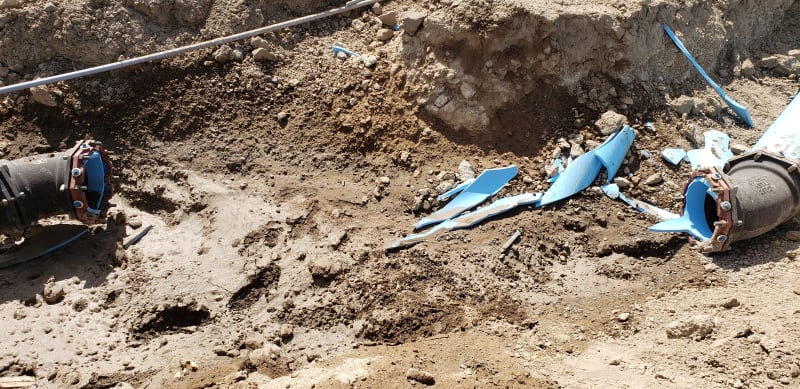