kanibaltaki
Industrial
heeey
i start to make a small tester mechanism I want to calculate the force applied by the driver with his foot on the clutch pedal and the spring because I want take this force and apply it with a pneumatic cylinder to measure the cable life see attached picture
thank you
i start to make a small tester mechanism I want to calculate the force applied by the driver with his foot on the clutch pedal and the spring because I want take this force and apply it with a pneumatic cylinder to measure the cable life see attached picture
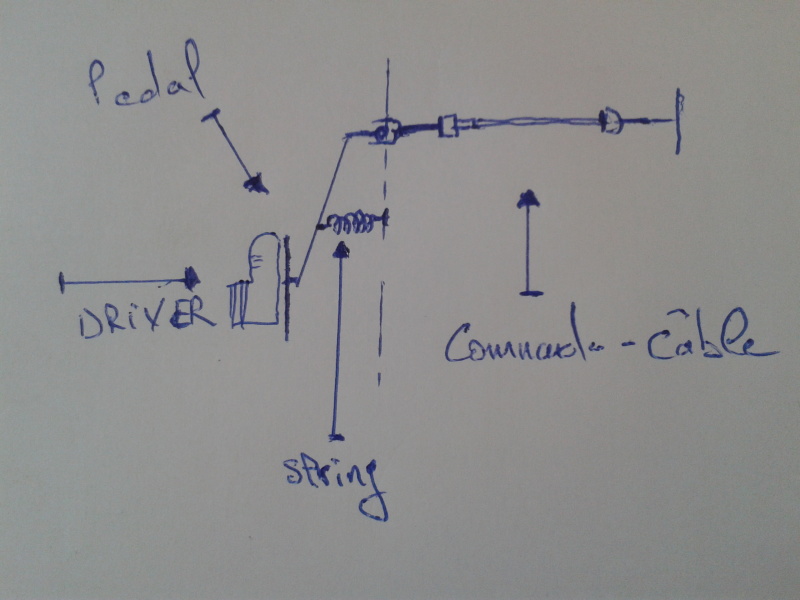
thank you