I perform a linear buckling analysis for two similar geometries, where one model has thickness t = 0.01 m, and the other has thickness t = 0.035 m. Otherwise everything is exactly the same. The thinner model (t = 0.01m) however gives me a higher critical buckling load compared to thicker model (t = 0.035m)- could this be right? The slope in the linear region or Young's Modulus for both models seem to correspond well with previous studies, it is just that I'm getting lower buckling load as I increase the thickness.
Edit: I had to increase the Dimensions of the Krylov space from 0 to 300 to capture any buckling modes for the t = 0.035 m model.
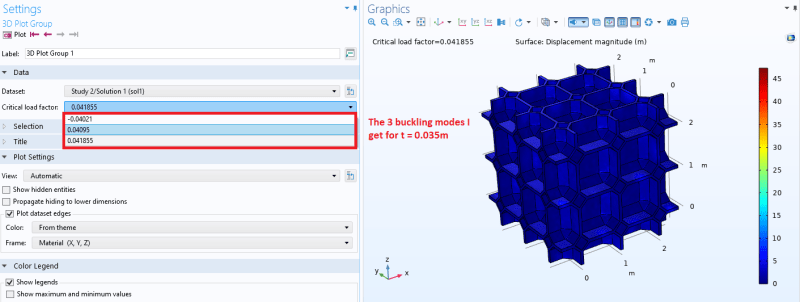
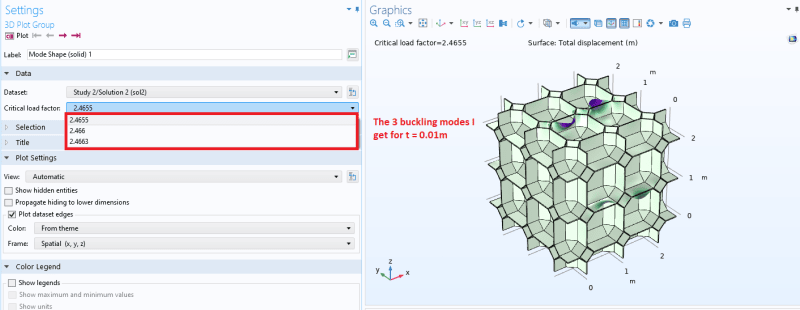
Edit: I had to increase the Dimensions of the Krylov space from 0 to 300 to capture any buckling modes for the t = 0.035 m model.