Imposter666
Mechanical
This lifter I have designed is lifting 100lb weight 300mm up from a surface and transferring it to another station. As you can see the the middle gripper is supported by LM guides at the ends. It is lifted by a single 80mm dia cylinder at the center. Originally I had 2 equal sized cylinders at each sides, but I was concerned that if one cylinder moves slower due to deteriorated seal or something, it might cause jamming on the LM guides due to imbalance of forces. I am personally not a big fan of this single cylinder sticking out like an antenna in the middle. I was wondering if there is a way to make 2 small side cylinder work instead of this big center cylinder.
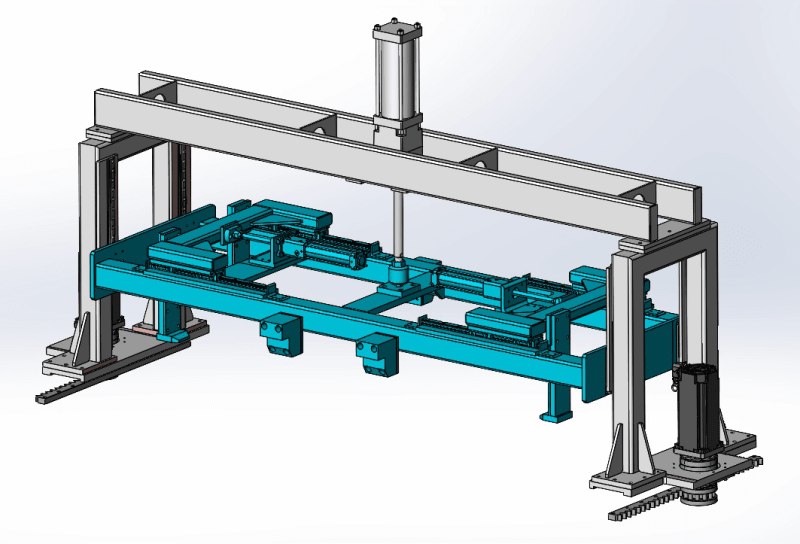
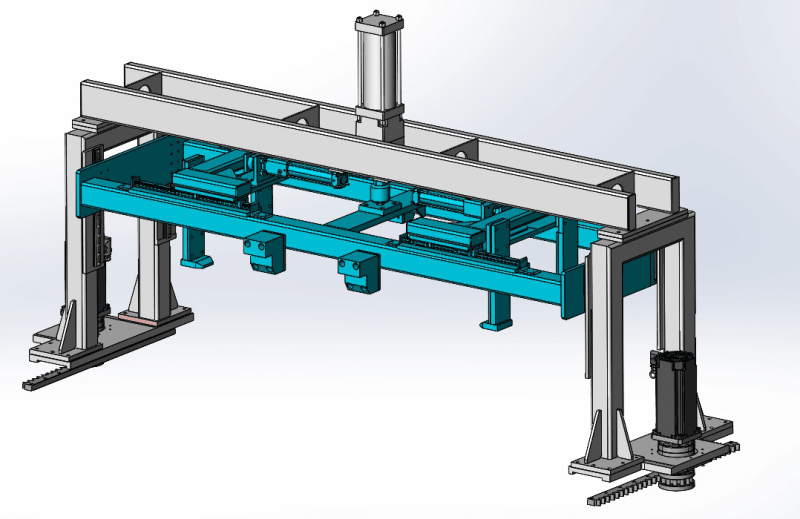