Good day,
I'm designing a built-up crane runway beam built of the w-section and a c-channel welded onto the top flange. When checking the built-up member top flange elements for their class/compactness, I'm not sure what criteria to use for the part of the c-channel web located between the edge of the top flange of the w-section and the edge of the c-channel. I think it is a similar case to where the compression flange is supported on two edges with welds/fasteners but just wanted to see if there are other opinions. My assumed scenario would require it to be checked for the following criteria: CSA S16:19 - bel/t<=420/sqrt(Fy); bel/t<=525/sqrt(Fy); bel/t<=670/sqrt(Fy); or AISC - b/t<=1.12xsqrt(E/Fy); b/t<=1.40xsqrt(E/Fy).
I attached the sketch showing which part of the c-channel I'm referring to.
Thanks for you input.
I'm designing a built-up crane runway beam built of the w-section and a c-channel welded onto the top flange. When checking the built-up member top flange elements for their class/compactness, I'm not sure what criteria to use for the part of the c-channel web located between the edge of the top flange of the w-section and the edge of the c-channel. I think it is a similar case to where the compression flange is supported on two edges with welds/fasteners but just wanted to see if there are other opinions. My assumed scenario would require it to be checked for the following criteria: CSA S16:19 - bel/t<=420/sqrt(Fy); bel/t<=525/sqrt(Fy); bel/t<=670/sqrt(Fy); or AISC - b/t<=1.12xsqrt(E/Fy); b/t<=1.40xsqrt(E/Fy).
I attached the sketch showing which part of the c-channel I'm referring to.
Thanks for you input.
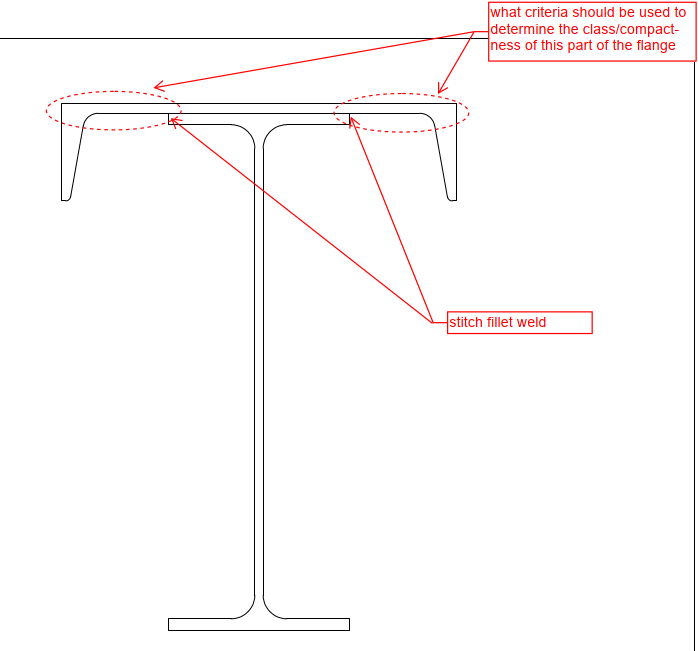