emonje
Mechanical
- Nov 3, 2006
- 48
Hello,
We make these cast steel tips for dragline buckets. Several failed recently, failure rate much higher than usual.
We had a batch of these tips hardfaced on top, front, side and bottom faces. Hardfacing didn't cover full face, just few ~20 mm wide weld lays of hardfacing metal.
All the failures have been in this batch.
Material is cast steel with Carbon equivalent of 0.7, typical hardness 400-450 BHN (43-47 HRC), typical yield strength around 750 MPa (108 ksi)
Here are some photos of the failed part:
Here's a rendering of the part with hardfacing:
Can anyone please shed some light on possible cause & remedy?
I don't have any info on how the hardfacing was done, if any pre-heat or PWHT applied.
I was thinking this overwhelmingly brittle fracture was because the part was cooled too quickly, making it too hard to the application.
Not sure if pre-heat will help, part is too small to hold heat & remain in high enough temperature may be?
I was more inclined to some form of PWHT after hardfacing, or at least put it in furnace for slow cooling.
Thanks.
We make these cast steel tips for dragline buckets. Several failed recently, failure rate much higher than usual.
We had a batch of these tips hardfaced on top, front, side and bottom faces. Hardfacing didn't cover full face, just few ~20 mm wide weld lays of hardfacing metal.
All the failures have been in this batch.
Material is cast steel with Carbon equivalent of 0.7, typical hardness 400-450 BHN (43-47 HRC), typical yield strength around 750 MPa (108 ksi)
Here are some photos of the failed part:
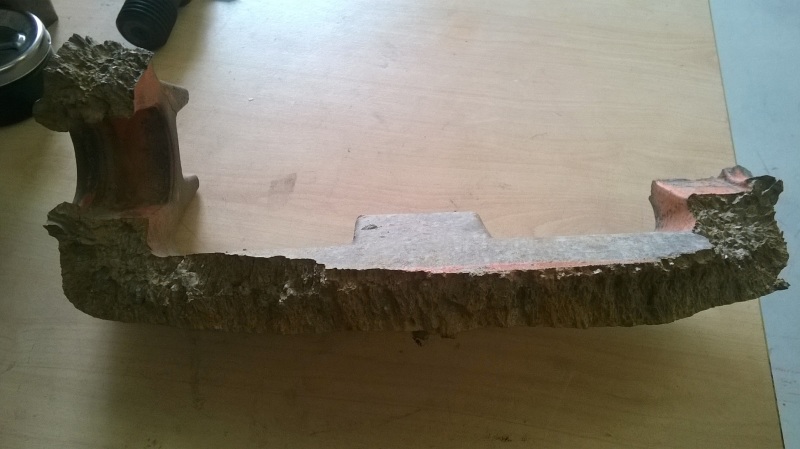
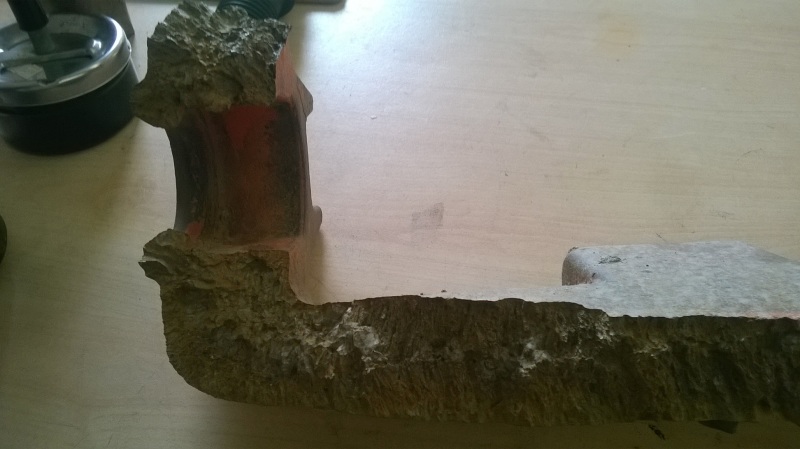
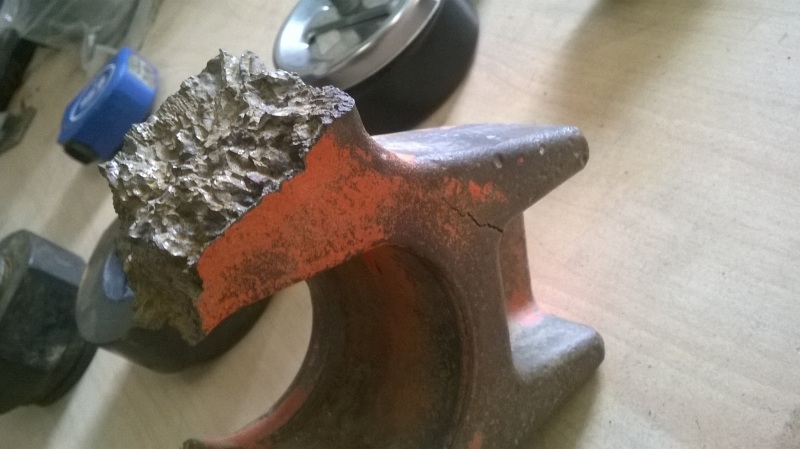
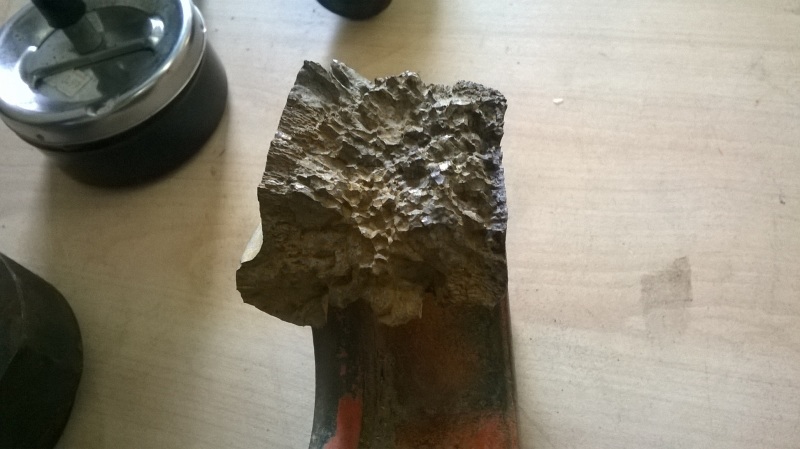
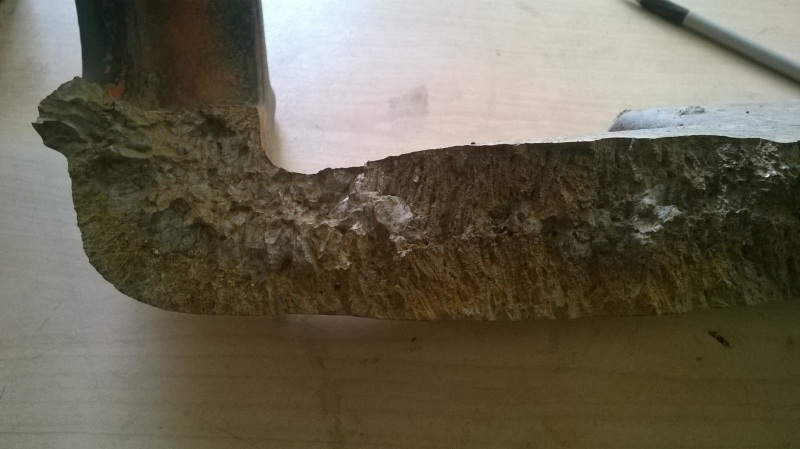
Here's a rendering of the part with hardfacing:
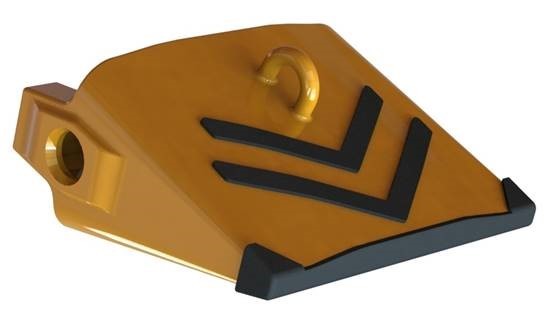
Can anyone please shed some light on possible cause & remedy?
I don't have any info on how the hardfacing was done, if any pre-heat or PWHT applied.
I was thinking this overwhelmingly brittle fracture was because the part was cooled too quickly, making it too hard to the application.
Not sure if pre-heat will help, part is too small to hold heat & remain in high enough temperature may be?
I was more inclined to some form of PWHT after hardfacing, or at least put it in furnace for slow cooling.
Thanks.