PSR_1
Civil/Environmental
- Aug 9, 2016
- 56
A paper by kenneth B. Bondy titled "Two way post-tensioned slabs with bonded tendons" has some interesting description about catenary effect associated with unbonded PT( see the highlighted part in the picture.
I want to see if this claim is sound and logical.
I want to see if this claim is sound and logical.
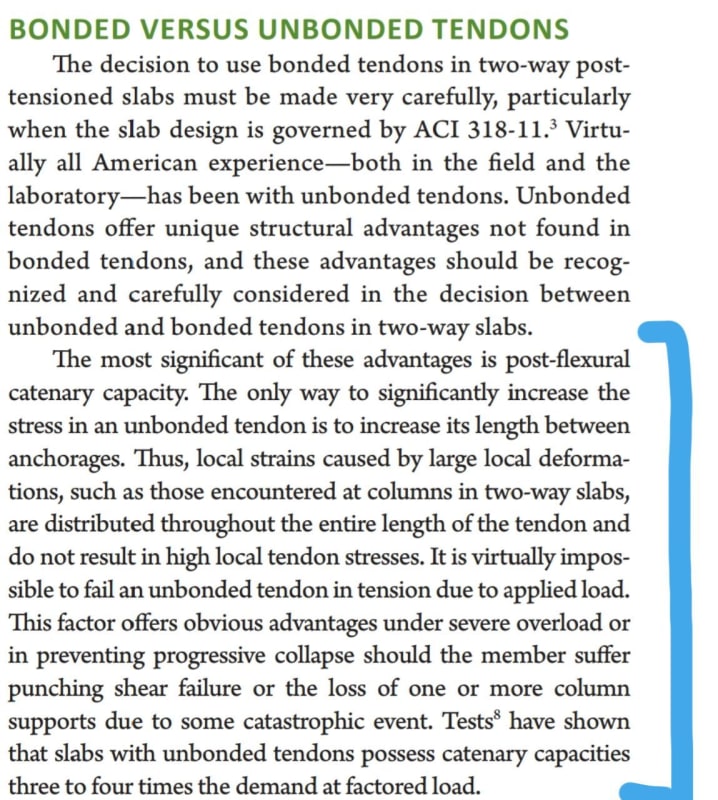