struct_eeyore
Structural
I have 2 small embed plates, 5x8x1/2 w/ 2 closely spaced headed studs at the end of a stub concrete cantilever. The embeds a staggered to fit roughly opp. of each other. The entire load carried by these two plates is about 600lb when the small section of roof they carry is fully loaded, otherwise it only supports about 250 lb. This is still in construction, and I got some lovely photos earlier today with a big old crack right down the centerline of the headed studs (see image)
Let's for a second ignore that the top reinforcing was not installed and hooked to contain everything. Then, even with the eccentrically loaded condition, my truncated prism failure is on an order of magnitude higher than the demand, as is the plain concrete moment capacity and shear accounting for the reduction in cross section where the studs are located. So I'm really struggling to determine the cause of failure here. From one side, a 20'L channel frames in, from the other a 7' channel - could this be driven by thermal expansion? I've yet to go to the site, but it looks like there's an angle between the south beam and the embed - prying action maybe?
Open to any and all feedback.
Let's for a second ignore that the top reinforcing was not installed and hooked to contain everything. Then, even with the eccentrically loaded condition, my truncated prism failure is on an order of magnitude higher than the demand, as is the plain concrete moment capacity and shear accounting for the reduction in cross section where the studs are located. So I'm really struggling to determine the cause of failure here. From one side, a 20'L channel frames in, from the other a 7' channel - could this be driven by thermal expansion? I've yet to go to the site, but it looks like there's an angle between the south beam and the embed - prying action maybe?
Open to any and all feedback.
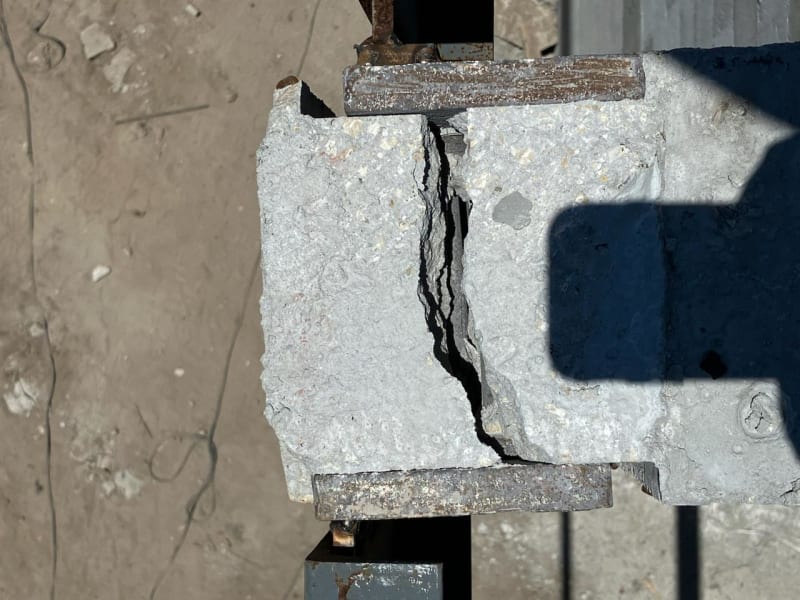