Hi!
I have a pump that serves a cooling tower. It was designed for 340GPM and 68 feet of head. In the installed condition, it is moving the 335GPM but head pressure is on 43 feet and its VFD is running at 45 HZ (2832RPM, max speed is 3600RPM). At the pump inlet the pressure is barely 1PSI, and the pump has cavitated.
I was not there for the balancing so I am assuming the balancer ran the pump at 60Hz, got too much flow, and they slowed the pump down. Was that the incorrect thing to do? Is the pump size incorrect (68 feet design but only 43 feet drop in the system) How can I keep my flow but get my head pressure up so I don't cavitate?
Here is the design curve, and the operating curve.
I have a pump that serves a cooling tower. It was designed for 340GPM and 68 feet of head. In the installed condition, it is moving the 335GPM but head pressure is on 43 feet and its VFD is running at 45 HZ (2832RPM, max speed is 3600RPM). At the pump inlet the pressure is barely 1PSI, and the pump has cavitated.
I was not there for the balancing so I am assuming the balancer ran the pump at 60Hz, got too much flow, and they slowed the pump down. Was that the incorrect thing to do? Is the pump size incorrect (68 feet design but only 43 feet drop in the system) How can I keep my flow but get my head pressure up so I don't cavitate?
Here is the design curve, and the operating curve.
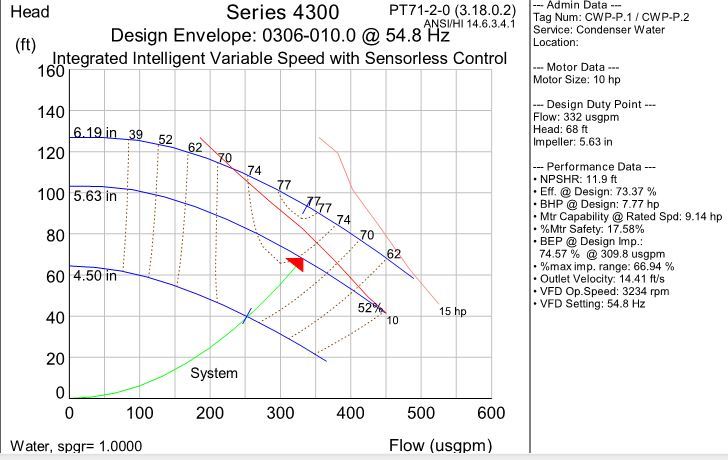
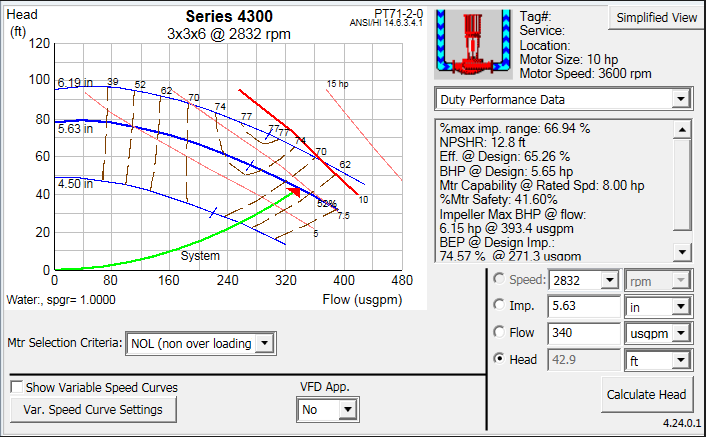