kookypedia
Electrical
- Jun 9, 2016
- 62
Guys,
I have 26 KA ground fault to be taken care by ground grid. I have put so much copper and rods but it doesn't change that much. Should I put ground well or anything else?
Any help would be appreciated,
I have 26 KA ground fault to be taken care by ground grid. I have put so much copper and rods but it doesn't change that much. Should I put ground well or anything else?
Any help would be appreciated,
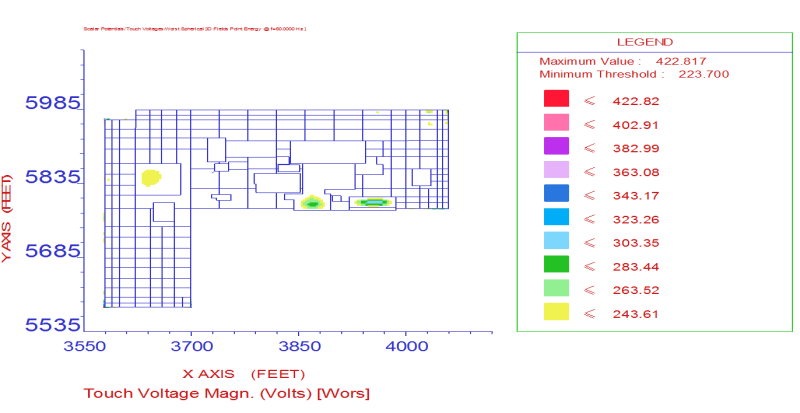