StrEng007
Structural
- Aug 22, 2014
- 543
I found a CFSEI Technical Note that discusses bracing for light gauge studs. One particular section seems to go against the consensus that I've read here.
The generally accepted idea being that, providing sheathing on wall studs would cut down the unbraced length for axial loads.
This is disputed by the note that brings up a topic I haven't seen discussed here before:
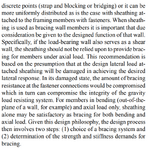
"if the load-bearing wall also serves as a shear wall, the sheathing should not be relied upon to provide bracing for members under axial load."
With that being said, I'm sure that a majority of exterior load bearing walls also serve as shear walls. Also, no matter what direction the MWFRS wind is blowing, you're always going to have either windward, leeward, or side wall pressures. So should we really be designing walls studs as being COMPLETELY UNBRACED for both gravity and lateral loads? How can an exterior load bearing wall ever really be subjected to ONLY bending or axial?
The generally accepted idea being that, providing sheathing on wall studs would cut down the unbraced length for axial loads.
This is disputed by the note that brings up a topic I haven't seen discussed here before:
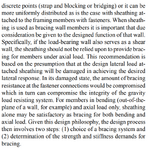
"if the load-bearing wall also serves as a shear wall, the sheathing should not be relied upon to provide bracing for members under axial load."
With that being said, I'm sure that a majority of exterior load bearing walls also serve as shear walls. Also, no matter what direction the MWFRS wind is blowing, you're always going to have either windward, leeward, or side wall pressures. So should we really be designing walls studs as being COMPLETELY UNBRACED for both gravity and lateral loads? How can an exterior load bearing wall ever really be subjected to ONLY bending or axial?