I am upgrading a shipboard crane hydraulic system.
The crane has overboard swing frame at the end of the Jib to securely latch into an ROV during launch and recovery.
The swing frame has 4 X single acting, single pistons hydraulically actuated by a three way ball valve and a pressure reducing valve.
The idea is that the brakes can be applied by opening the three way ball valve and adjusting the reducing valve to the desired brake drag. The brakes can then be locked at the desired pressure. The brakes are released by turning the ball valve to the third position which routes oil from the brake calipers to tank.
The problem that has arisen, is that the new system is load sensing. The standby pressure is 300 PSI but we require up to 1200 PSI for the brake pressure.
When the brake is applied and locked, the pressure will bleed off slowly though the LS line.
Unfortunately, we need the brake to hold and/or release even without hydraulic pressure.
I have attached a partial Schematic for clarity
Thanks
Peter
The crane has overboard swing frame at the end of the Jib to securely latch into an ROV during launch and recovery.
The swing frame has 4 X single acting, single pistons hydraulically actuated by a three way ball valve and a pressure reducing valve.
The idea is that the brakes can be applied by opening the three way ball valve and adjusting the reducing valve to the desired brake drag. The brakes can then be locked at the desired pressure. The brakes are released by turning the ball valve to the third position which routes oil from the brake calipers to tank.
The problem that has arisen, is that the new system is load sensing. The standby pressure is 300 PSI but we require up to 1200 PSI for the brake pressure.
When the brake is applied and locked, the pressure will bleed off slowly though the LS line.
Unfortunately, we need the brake to hold and/or release even without hydraulic pressure.
I have attached a partial Schematic for clarity
Thanks
Peter
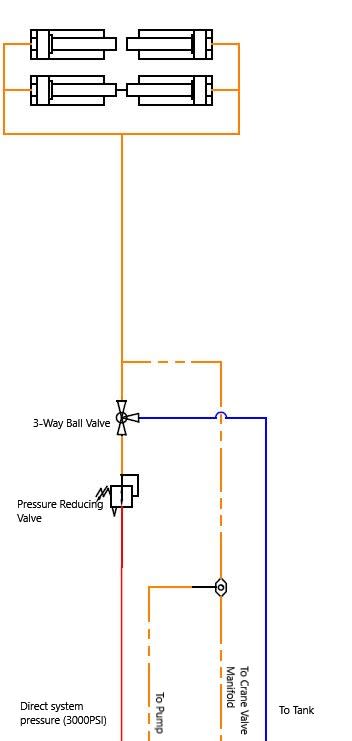