dejan95
Mechanical
- Aug 24, 2020
- 60
Hello everyone,
I have a simple question. I'm mechanical design engineer beginner and I'm wondering, is it better to design parts with fillets or with chamfers?
Bellow are a couple of examples.
Thank you for your help and have a happy holidays!
I have a simple question. I'm mechanical design engineer beginner and I'm wondering, is it better to design parts with fillets or with chamfers?
Bellow are a couple of examples.
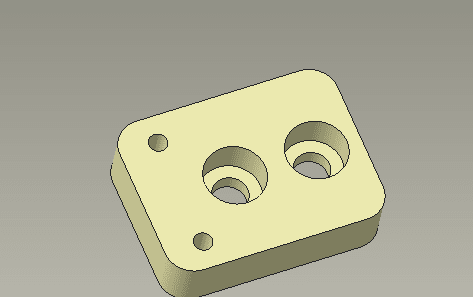
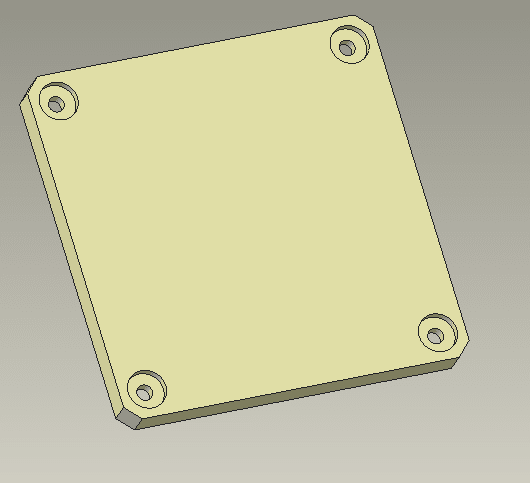
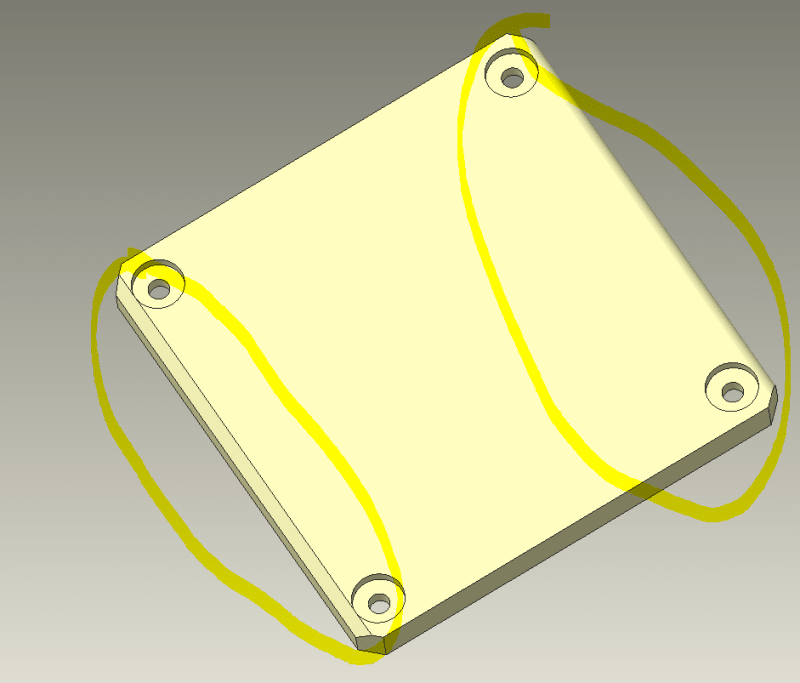
Thank you for your help and have a happy holidays!