Whoopdedo_LSU
Structural
- Apr 27, 2017
- 35
I have a question involving welding. I am welded a 4x3 member to a 6x3 member. I cannot get a weld to work. From testing, it was found that we can only get 1/8" weld penetration from the groove weld. I am wondering if I can add a "stiffener" in to get extra weld length.
The left is a plan view and the right is elevation.
If I can use this extra weld length from the stiffener, how would I treat that added weld area?
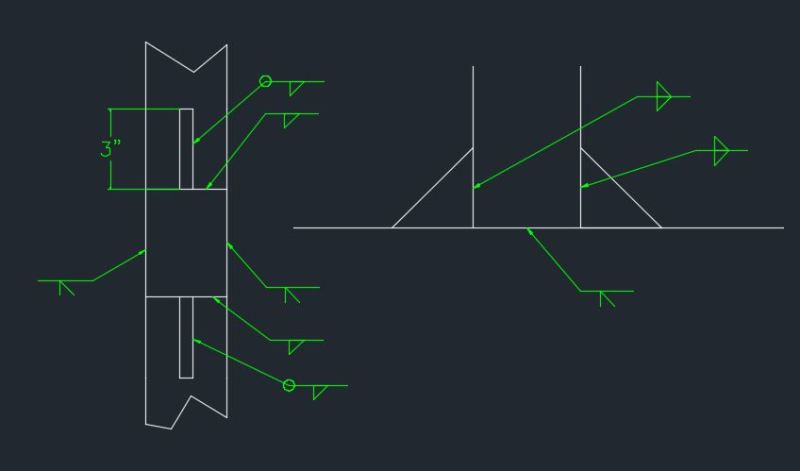
The left is a plan view and the right is elevation.
If I can use this extra weld length from the stiffener, how would I treat that added weld area?