VaggelisKas
Industrial
- May 11, 2015
- 36
Hello community,
I have the following simulation problem.
I an trying to simulate a case of 2D orthogonal cutting.
The chip is normally created but when it curls up there is no interaction between the surfaces.
I have tried to use the self contact on the outermost surface of the workpiece but I get the error of the extreme deformation of
the elements.
Any ideas would be highly appreciated.
Thanks in advance.
I have the following simulation problem.
I an trying to simulate a case of 2D orthogonal cutting.
The chip is normally created but when it curls up there is no interaction between the surfaces.
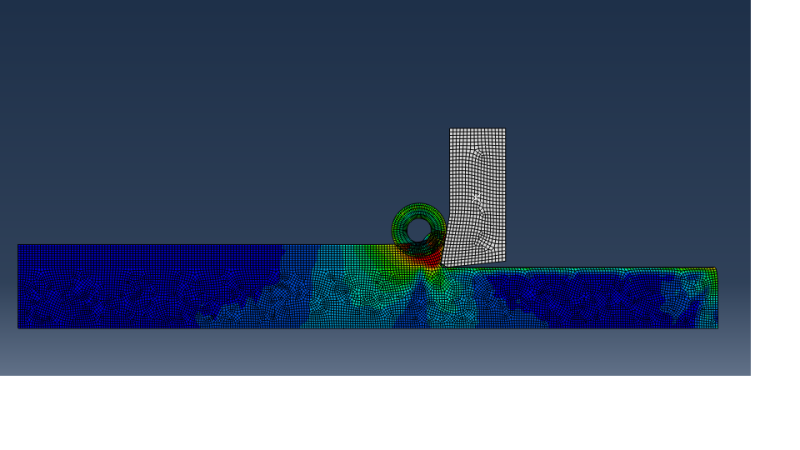
I have tried to use the self contact on the outermost surface of the workpiece but I get the error of the extreme deformation of
the elements.
Any ideas would be highly appreciated.
Thanks in advance.