Hello everyone. I am a young mechanical engineer at his first job and, not being supported by any tutor, I really need to get advice from some more experienced colleagues.
In particular, I would like to ask you for advice on choosing an electric motor. I should rotate a sort of "rotisserie" with an eccentric center of gravity with respect to the rotation axis (photo attached). The whole will weigh about 500 kg. The rotation can also take place slowly as long as the four desired positions with an increase of rotation of 90 ° are extremely accurate as the piece must be machined by a laser in all four positions that will follow. Consequently, the service will be of an intermittent type with running phases (rotation of 90 °) and stop which are repeated alternately.
Given the high precision required and the weight of the object, I thought of orienting myself on a brushless servo going to compensate for the low rotation speeds (which could annoy this type of motor) with the insertion of a gearbox.
A possible alternative could be an asynchronous motor with feedback control. It should be less expensive than a brushless and easier to implement at the control logic level. In this case, however, I am concerned by the fact that the torque to be supplied by the motor will not be constant but, since the center of gravity is eccentric with respect to the axis, it will vary according to the position of the latter.
Finally, there is the possibility of the stepper. Even in this case, however, one with closed-chain control would be needed to avoid the risk of losing the step. But I don't know if it could be suitable with the weights involved.
In short, as you can see, I am a bit confused about what to do and would really appreciate the opinion of some colleagues
In particular, I would like to ask you for advice on choosing an electric motor. I should rotate a sort of "rotisserie" with an eccentric center of gravity with respect to the rotation axis (photo attached). The whole will weigh about 500 kg. The rotation can also take place slowly as long as the four desired positions with an increase of rotation of 90 ° are extremely accurate as the piece must be machined by a laser in all four positions that will follow. Consequently, the service will be of an intermittent type with running phases (rotation of 90 °) and stop which are repeated alternately.
Given the high precision required and the weight of the object, I thought of orienting myself on a brushless servo going to compensate for the low rotation speeds (which could annoy this type of motor) with the insertion of a gearbox.
A possible alternative could be an asynchronous motor with feedback control. It should be less expensive than a brushless and easier to implement at the control logic level. In this case, however, I am concerned by the fact that the torque to be supplied by the motor will not be constant but, since the center of gravity is eccentric with respect to the axis, it will vary according to the position of the latter.
Finally, there is the possibility of the stepper. Even in this case, however, one with closed-chain control would be needed to avoid the risk of losing the step. But I don't know if it could be suitable with the weights involved.
In short, as you can see, I am a bit confused about what to do and would really appreciate the opinion of some colleagues
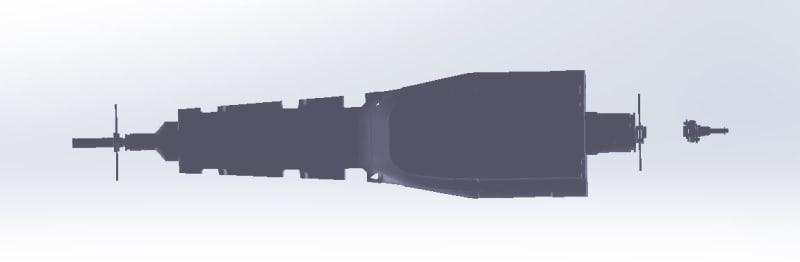