I've modeled a rectangular tube being clamped via a pretensioned bolt:
The tube is 10 mm thick (steel) and is fixed at one end. The pretension force is 50 kN.
I also modeled a 50 kN nodally-distributed force on the washers of another connection, to compare the results:
The contacts between the components are set to "friction" with a coefficient of 0.7:
The simulation is a non-linear static analysis.
The stress results are very large. Especially around the hole edge:
I realize that 660 MPa is an overestimation as the stress is beyond the yield stress. But these results suggest yielding around the hole.
Additionally, the deformation results show a deformation of 0.2 mm at the hole edge:
However, just from experience/intuition, it is obvious that torquing a bolt to spec (50 kN clamp load) will not cause a 10 mm thick tube to yield.
I had a test done. After torquing the bolt 50 kN, the bolt deflected 0.1 mm (not 0.2 mm as predicted by the simulation). Upon release, the tube sprang back with no evidence of plastic deformation.
Why are the simulation results much larger than reality?
How should I accurately simulate this configuration?
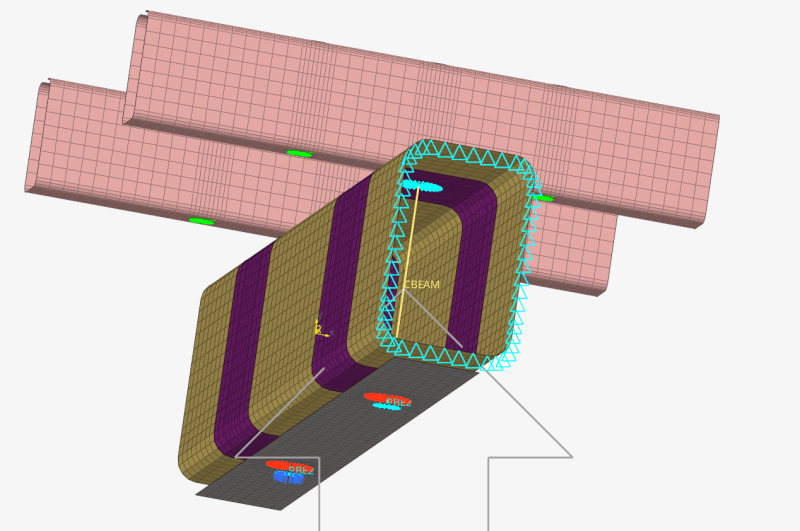
The tube is 10 mm thick (steel) and is fixed at one end. The pretension force is 50 kN.
I also modeled a 50 kN nodally-distributed force on the washers of another connection, to compare the results:
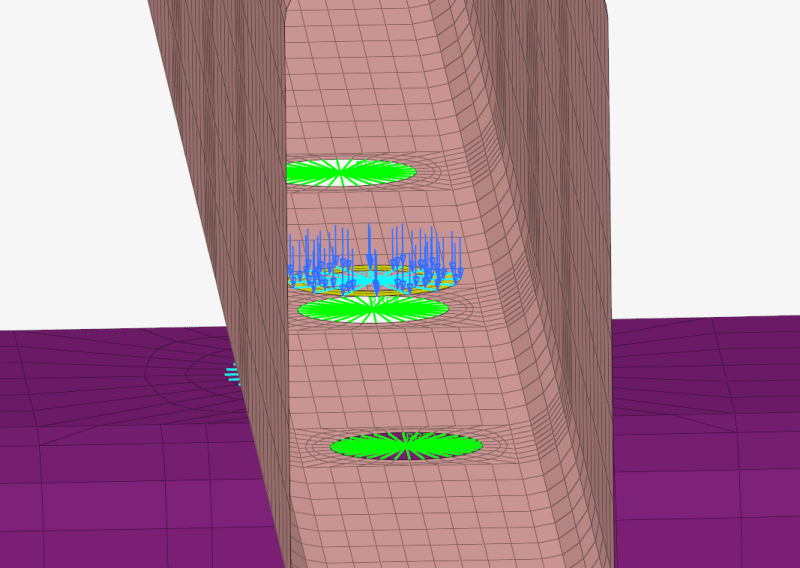
The contacts between the components are set to "friction" with a coefficient of 0.7:
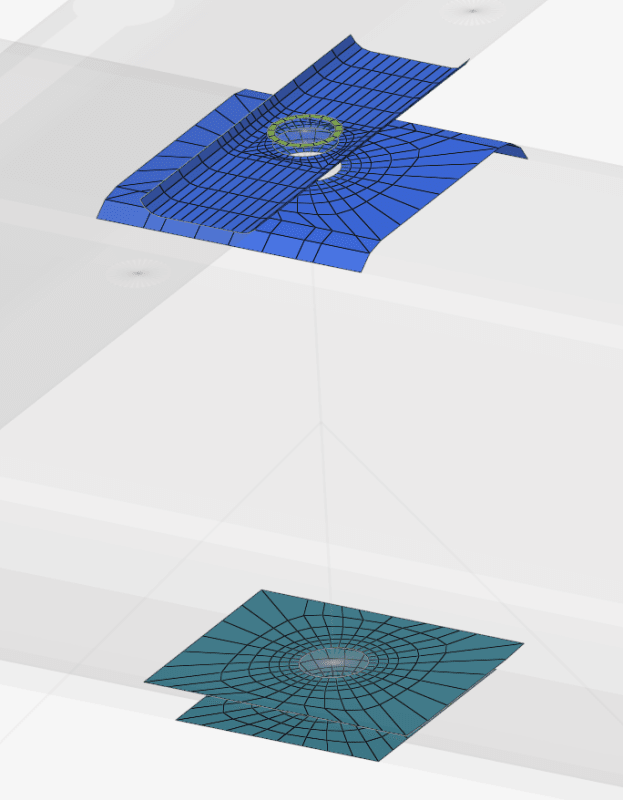
The simulation is a non-linear static analysis.
The stress results are very large. Especially around the hole edge:

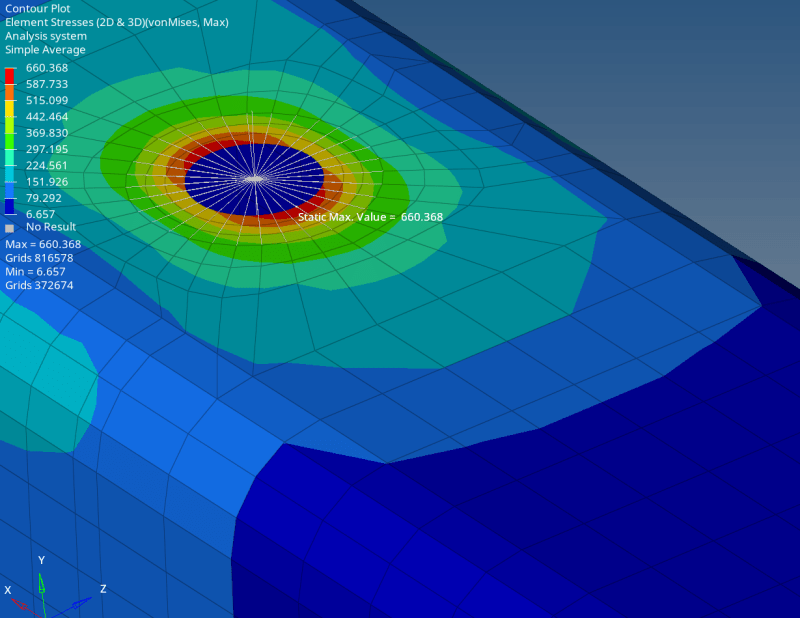
I realize that 660 MPa is an overestimation as the stress is beyond the yield stress. But these results suggest yielding around the hole.
Additionally, the deformation results show a deformation of 0.2 mm at the hole edge:
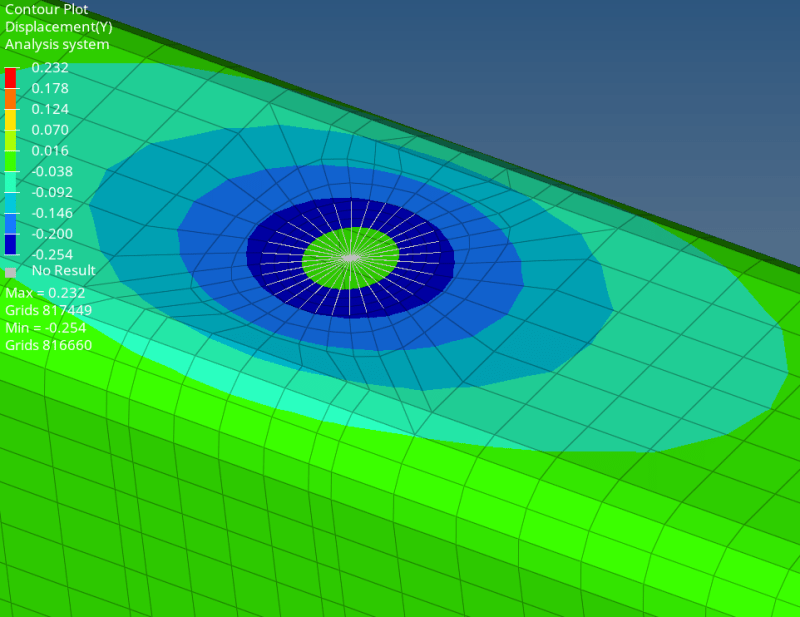
However, just from experience/intuition, it is obvious that torquing a bolt to spec (50 kN clamp load) will not cause a 10 mm thick tube to yield.
I had a test done. After torquing the bolt 50 kN, the bolt deflected 0.1 mm (not 0.2 mm as predicted by the simulation). Upon release, the tube sprang back with no evidence of plastic deformation.
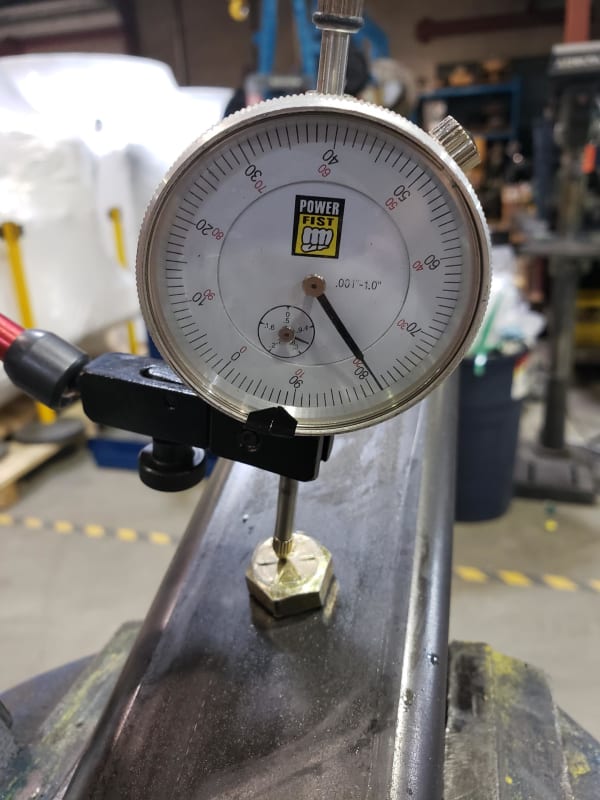
Why are the simulation results much larger than reality?
How should I accurately simulate this configuration?