Hi,
I am working as an mechanical engineer in a mining design firm. We have designed a shiploader that lifts and lowers the boom of the shiploader by means of a hydraulic cylinder. What makes this case special is the cylinder is connected to a pantograph meaning the load is not linear during the luffing cycle. I have included a sample of the varying load diagram for your reference below. We are using a closed loop hydraulic circuit with a axial piston variable pump.
The cylinder that we are using has a has dummy rod on the one side (also in the image attached), therefore we have a pressure ratio of 1:1 across the piston. Seeing that it is a closed loop hydraulic circuit the oil flows directly from the luffing cylinder directly to the pump at the same rate it leaves the hydraulic cylinder (pressure ration 1:1 across the piston). I understand the dynamics of regenerating electrical power making use of a pump which overturns the synchronous motor above the synchronous speed +- slippage and then the motor becomes a generator.
What I struggle to understand with the system, if the pump is delivering oil at a rate of Xm/s to the luffing cylinder on the one side while the cylinder pushes oil out at the other side at the same rate it receives due to the pressure ratio of 1:1 across the piston, the pump will again receive oil at the same rate due to the closed loop system. I therefore assume the oil is recirculating at the same velocity within the system. How can the pump start to turn fast in order to speed up the synchronous motor to generate power? Because the mass flow across the pump is constant.
I would really appreciate some guidance here.
Thanks a lot.
I am working as an mechanical engineer in a mining design firm. We have designed a shiploader that lifts and lowers the boom of the shiploader by means of a hydraulic cylinder. What makes this case special is the cylinder is connected to a pantograph meaning the load is not linear during the luffing cycle. I have included a sample of the varying load diagram for your reference below. We are using a closed loop hydraulic circuit with a axial piston variable pump.
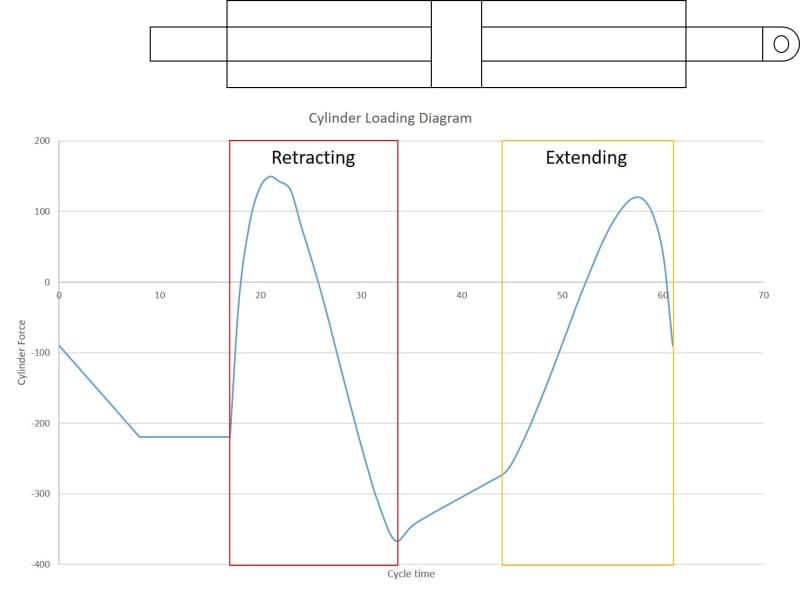
The cylinder that we are using has a has dummy rod on the one side (also in the image attached), therefore we have a pressure ratio of 1:1 across the piston. Seeing that it is a closed loop hydraulic circuit the oil flows directly from the luffing cylinder directly to the pump at the same rate it leaves the hydraulic cylinder (pressure ration 1:1 across the piston). I understand the dynamics of regenerating electrical power making use of a pump which overturns the synchronous motor above the synchronous speed +- slippage and then the motor becomes a generator.
What I struggle to understand with the system, if the pump is delivering oil at a rate of Xm/s to the luffing cylinder on the one side while the cylinder pushes oil out at the other side at the same rate it receives due to the pressure ratio of 1:1 across the piston, the pump will again receive oil at the same rate due to the closed loop system. I therefore assume the oil is recirculating at the same velocity within the system. How can the pump start to turn fast in order to speed up the synchronous motor to generate power? Because the mass flow across the pump is constant.
I would really appreciate some guidance here.
Thanks a lot.