shacked
Structural
- Aug 6, 2007
- 176
I am designing a HSS beam used for a residential stair. It will be a single HSS stringer cold bent to an approximate 4ft inside radius and span from ground floor to 2nd floor. I have never designed a steel beam that is bent in 2 directions like this is, so I have a few questions.
Are any of the steels physical properties changed after bending, such as yield stress?
IF anyone has designed this type of beam what would you suggest that I design each of the end supports for? Fully restrained both ends, pinned one end and fully restrained the other?
Or any information or direction as to where I find information about designing members like that would be greatly appreciated.
Sorry for the very basic plan, but this is what the architect provided
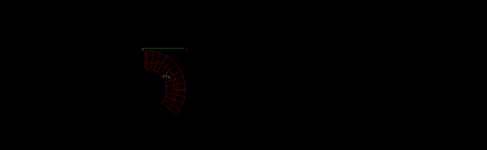
Are any of the steels physical properties changed after bending, such as yield stress?
IF anyone has designed this type of beam what would you suggest that I design each of the end supports for? Fully restrained both ends, pinned one end and fully restrained the other?
Or any information or direction as to where I find information about designing members like that would be greatly appreciated.
Sorry for the very basic plan, but this is what the architect provided
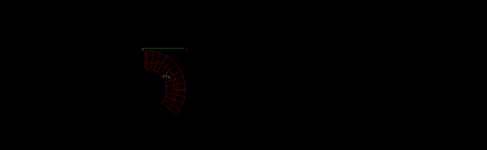