kellez
Civil/Environmental
- Nov 5, 2011
- 276
Hello everyone,
I am designing a 2storey RC frame house according to EC2 and EC8 and three of the columns are impossible to design.
Two of these columns 13 and 20 are of similar configuration, please see image below.
They have eccentric beams connected perpendicular to the column one at each end.
all columns fail at seismic load combinations
No matter how much shear reinforcement i add or how much i increase the column section it still fails at seismic combinations.
I tried researching why these 3 columns fail and i found out some excessive shear forces are generated at the seismic combinations reaching up to 1000kN in the strong axis of the column.
I think this is way excessive considering the fact that this is just a 2storey house and in fact the total base shear of the structure (in the design spectrum acceleration) is only about 900kN.
I am designing a 2storey RC frame house according to EC2 and EC8 and three of the columns are impossible to design.
Two of these columns 13 and 20 are of similar configuration, please see image below.
They have eccentric beams connected perpendicular to the column one at each end.
all columns fail at seismic load combinations
No matter how much shear reinforcement i add or how much i increase the column section it still fails at seismic combinations.
I tried researching why these 3 columns fail and i found out some excessive shear forces are generated at the seismic combinations reaching up to 1000kN in the strong axis of the column.
I think this is way excessive considering the fact that this is just a 2storey house and in fact the total base shear of the structure (in the design spectrum acceleration) is only about 900kN.
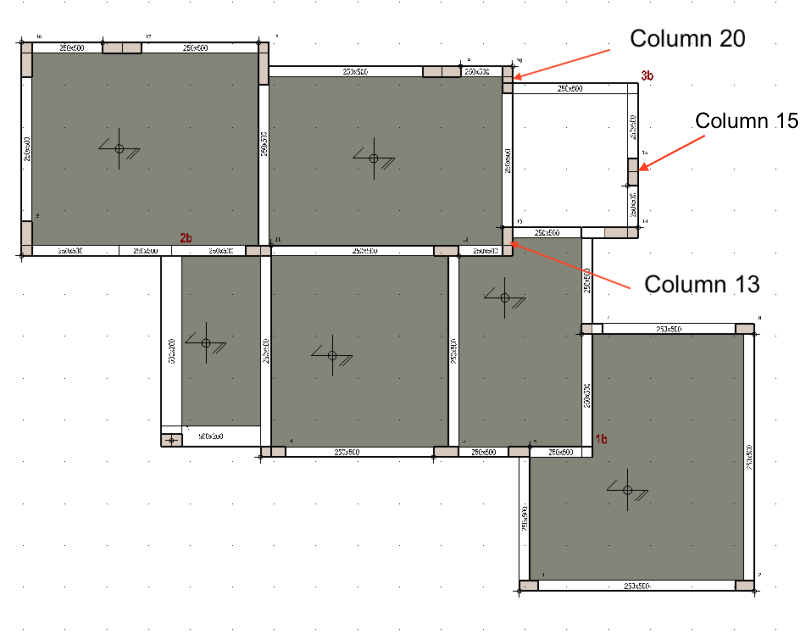
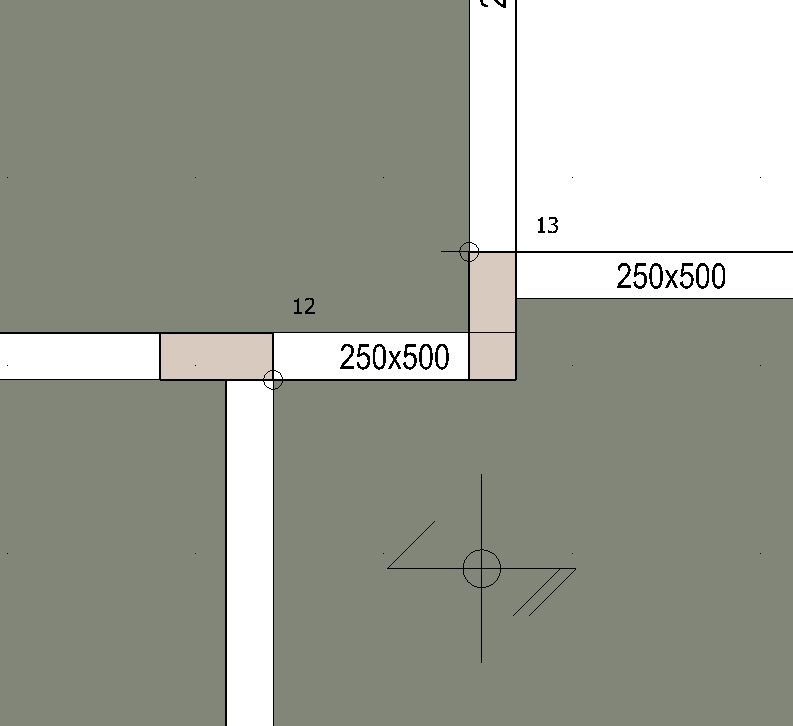
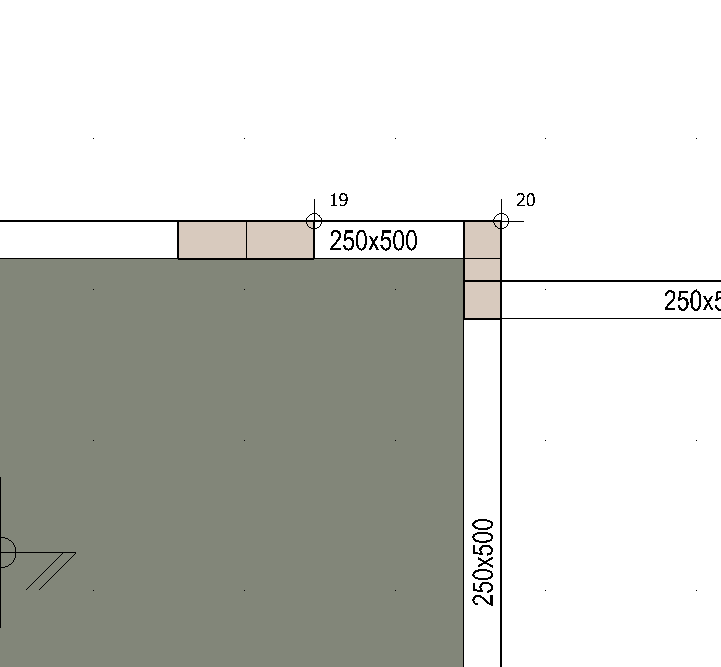