Amar Yarli
Structural
Hi,
I am checking a baseplate drawing where the column is stepped down in size at the baseplate connection (image attached) to avoid the requirement for a large moment connection and many bolts.
I have not received calculations yet. The steel structure is subjected to seismic and wind loading along with dead and live loads.
Please let me know if this any recommended practice for a simpler baseplate connection design.
Regards,
Amar
I am checking a baseplate drawing where the column is stepped down in size at the baseplate connection (image attached) to avoid the requirement for a large moment connection and many bolts.
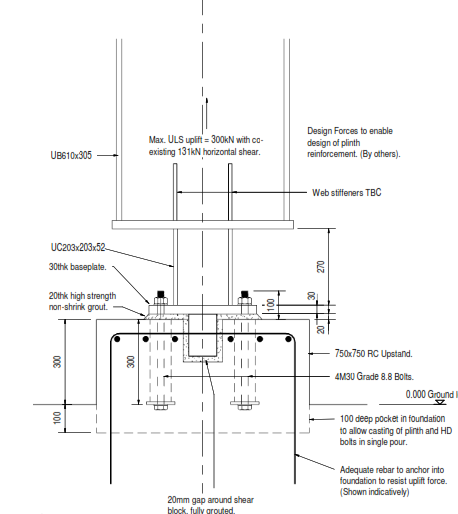
I have not received calculations yet. The steel structure is subjected to seismic and wind loading along with dead and live loads.
Please let me know if this any recommended practice for a simpler baseplate connection design.
Regards,
Amar