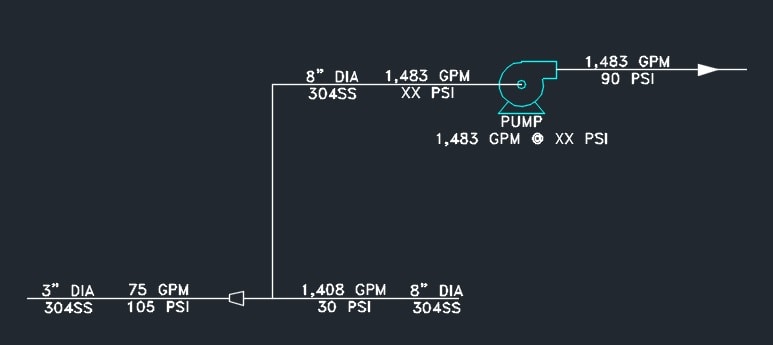
I'm trying to size a pump, but my issue is not being able to determining the feed pressure of said pump. I have a re circulation loop of 1,408 GPM. I am injecting 75 GPM into the loop at a higher pressure than the return loop pressure. Ultimately, the goal is to reduce the boost pressure required on the loop pump since the flow is so large. How much, if any, pressure can I make up with the injection?