Hi Everybody,
I am using RISA-3D for some bridge analysis, and I am having some difficulty with modeling composite behavior. I realize that RISA does not natively support composite analysis, but I am trying to find a way to make it work using rigid offsets to connect my deck elements (plates) to my beam elements.
I am designing a bridge with curved girders, and girder spacing that varies across the span. Because of the complex geometry of the framing plan, I would like to model the deck elements seperately from the girder elements using plates that change in width rather than having to put in a bunch of unique beam elements with different composite section properties all over the bridge.
I would also prefer the deck elements be separate so that I can use them to distribute loads across the deck to the different girder elements, as I need to account for the torsion on my curved members, and cannot just use AASHTO distribution factors.
I have started off by modeling a simple span beam with a point load in order to ensure that the program is behaving the way I expect. I am able to match the moments and shear with my hand calcs (The model results in bending in both the beam elements and the deck elements, along with an axial force couple in the 2 elements that resolve to the expected total moment), however I cannot match RISA's stress distribution in the beam elements. The value I am most interested in is the stress at the bottom flange, and this model is approximately 3% off from what it should be.
Here's the simple span model. I have 8" concrete plate elements (blue) connected to Tapered WF steel elements (Grey) with Rigid Offset elements (Green).
It's important that I can trust the stress values because the final geometry of the bridge will be pretty complex, and will make it extremely difficult to resolve member forces and calculate stress by hand.
I am wondering if anybody has had any luck using rigid offsets to create composite members in RISA. If so, what value did you use for rigid offset length (I have tried N.A. distance, COG distance, and 1/2 depth; and none have produced correct values)?
If nobody has had luck in RISA, I would ask if anybody has had better luck modeling composite behavior in a different program such as SAP2000, or CSI Bridge, that are in the ballpark of RISA in terms of cost.
Thanks for reading. Any help would be greatly appreciated.
I am using RISA-3D for some bridge analysis, and I am having some difficulty with modeling composite behavior. I realize that RISA does not natively support composite analysis, but I am trying to find a way to make it work using rigid offsets to connect my deck elements (plates) to my beam elements.
I am designing a bridge with curved girders, and girder spacing that varies across the span. Because of the complex geometry of the framing plan, I would like to model the deck elements seperately from the girder elements using plates that change in width rather than having to put in a bunch of unique beam elements with different composite section properties all over the bridge.
I would also prefer the deck elements be separate so that I can use them to distribute loads across the deck to the different girder elements, as I need to account for the torsion on my curved members, and cannot just use AASHTO distribution factors.
I have started off by modeling a simple span beam with a point load in order to ensure that the program is behaving the way I expect. I am able to match the moments and shear with my hand calcs (The model results in bending in both the beam elements and the deck elements, along with an axial force couple in the 2 elements that resolve to the expected total moment), however I cannot match RISA's stress distribution in the beam elements. The value I am most interested in is the stress at the bottom flange, and this model is approximately 3% off from what it should be.
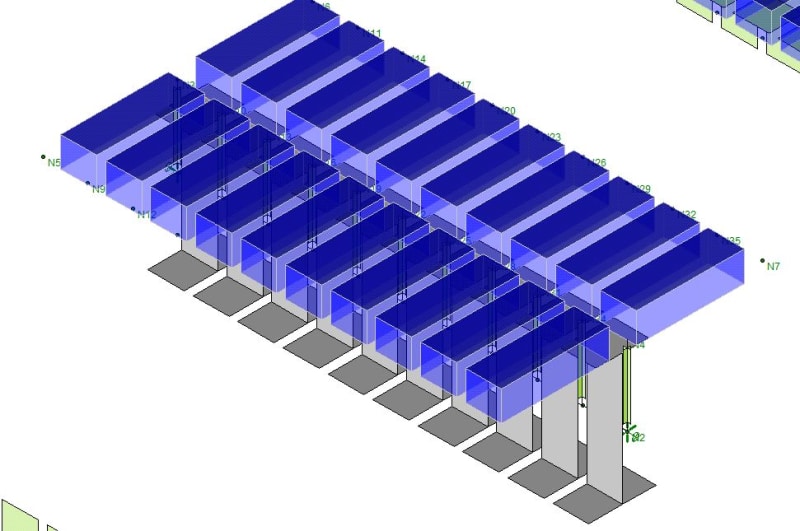
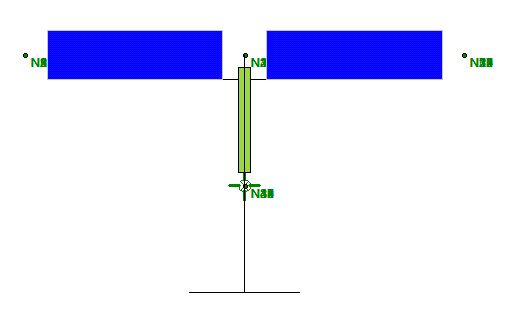
Here's the simple span model. I have 8" concrete plate elements (blue) connected to Tapered WF steel elements (Grey) with Rigid Offset elements (Green).
It's important that I can trust the stress values because the final geometry of the bridge will be pretty complex, and will make it extremely difficult to resolve member forces and calculate stress by hand.
I am wondering if anybody has had any luck using rigid offsets to create composite members in RISA. If so, what value did you use for rigid offset length (I have tried N.A. distance, COG distance, and 1/2 depth; and none have produced correct values)?
If nobody has had luck in RISA, I would ask if anybody has had better luck modeling composite behavior in a different program such as SAP2000, or CSI Bridge, that are in the ballpark of RISA in terms of cost.
Thanks for reading. Any help would be greatly appreciated.