sticksandtriangles
Structural
- Apr 7, 2015
- 494
Hello,
I have a condition where I am trying to ensure composite bending for an existing piece of wood sistered on each end with (2) LVLs.
See Below:
I know that the composite action is based on shear flow: v=VQ/I.
I wanted to design the fasteners to ensure composite action and wanted to confirm my design assumption of Q:
I also wanted to confirm that the equation, v=VQ/I, is showing me that adding more screws, e.g. maybe (4) rows of screws,
would not reduce my demand on the the upper screws.
I always note things where adding more does not help the situation. Let me know if I am missing something in the mix here.
Thanks for your thoughts in advance!
I have a condition where I am trying to ensure composite bending for an existing piece of wood sistered on each end with (2) LVLs.
See Below:
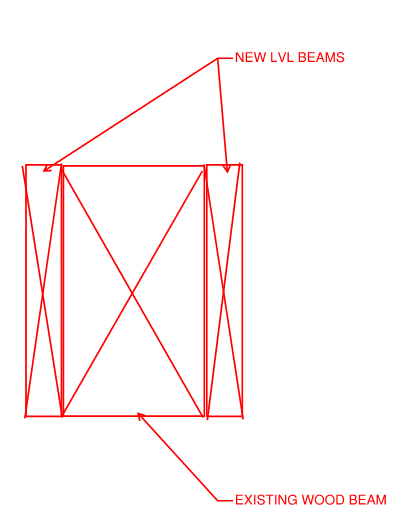
I know that the composite action is based on shear flow: v=VQ/I.
I wanted to design the fasteners to ensure composite action and wanted to confirm my design assumption of Q:
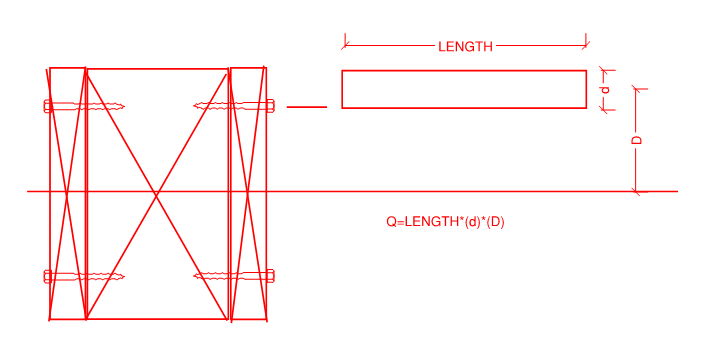
I also wanted to confirm that the equation, v=VQ/I, is showing me that adding more screws, e.g. maybe (4) rows of screws,
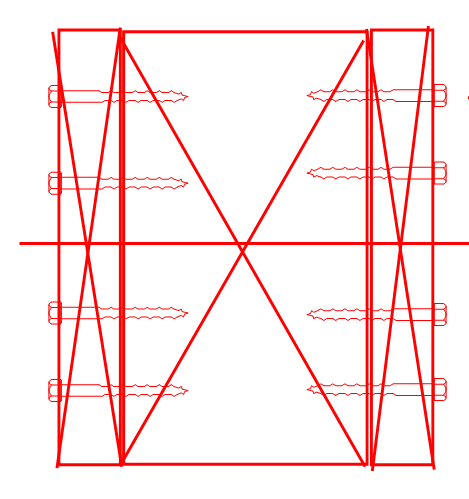
would not reduce my demand on the the upper screws.
I always note things where adding more does not help the situation. Let me know if I am missing something in the mix here.
Thanks for your thoughts in advance!