A query I could do with some help on (most likely basic fluid dynamics but struggling!)
Situation:
An industrial tool requires a small high pressure air chamber (1000 PSI+) an electrically controlled valve (currently a solenoid but could be something else) and an outlet pipe (1/4"). The valve needs to open extrmely quickly to allow the max amount of pressure in a short space of time to flow out through the outlet pipe (ideally expel all the air from the chamber at once).
a. The setup currently has a 1/2" steel pipe air chamber, 1/2" solenoid valve, a reducer and then 1/4" outlet pipe. The only part that has to remain a constant is the 1/4" outlet pipe. (see pic: air chamber on the right)
Larger aperture solenoid valves are limited in the max pressure they can handle. I tried a 1/4" solenoid (with 1/2" air chamber) but that struggled to expel sufficient air in one go - due to the restriction of going from 1/2 - 1/4 before the valve.
My queries are:
1. What would be the optimum setup to provide the maximum air flow (at high pressure) to the outlet pipe? Would keeping all elements at the same diameter (1/4") enable greater pressure at the outlet pipe, or is it better to go from a larger air chamber and valve (1" or 1/2") to the smaller outlet pipe (Venturi affect?).
2. Can anyone recommend a compact alternative to a solenoid valve that is both electrically operated and fast opening?
Any thoughts would be greatly appreciated!
Situation:
An industrial tool requires a small high pressure air chamber (1000 PSI+) an electrically controlled valve (currently a solenoid but could be something else) and an outlet pipe (1/4"). The valve needs to open extrmely quickly to allow the max amount of pressure in a short space of time to flow out through the outlet pipe (ideally expel all the air from the chamber at once).
a. The setup currently has a 1/2" steel pipe air chamber, 1/2" solenoid valve, a reducer and then 1/4" outlet pipe. The only part that has to remain a constant is the 1/4" outlet pipe. (see pic: air chamber on the right)
Larger aperture solenoid valves are limited in the max pressure they can handle. I tried a 1/4" solenoid (with 1/2" air chamber) but that struggled to expel sufficient air in one go - due to the restriction of going from 1/2 - 1/4 before the valve.
My queries are:
1. What would be the optimum setup to provide the maximum air flow (at high pressure) to the outlet pipe? Would keeping all elements at the same diameter (1/4") enable greater pressure at the outlet pipe, or is it better to go from a larger air chamber and valve (1" or 1/2") to the smaller outlet pipe (Venturi affect?).
2. Can anyone recommend a compact alternative to a solenoid valve that is both electrically operated and fast opening?
Any thoughts would be greatly appreciated!
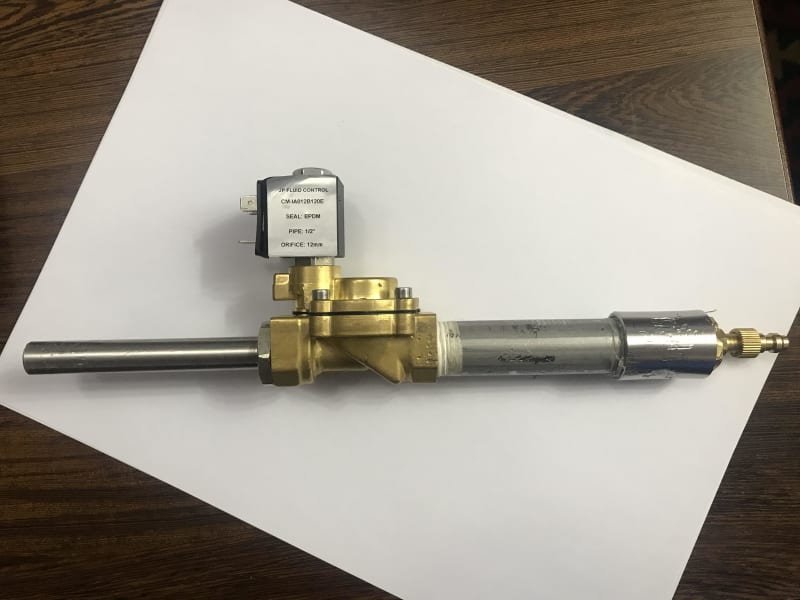