Hello,
Lets say i have the situation in the image below.
Lets say that the stress in the column is near yielding. The compression force has to go trough the plate, then the flange and then the stiffeners down to the other column.
Wouldnt this mean that the flange under the column is also close to yielding and any bending moment added to the beam would result in failure of the beam. because these stresses need to be combined? Or does this effect not have to be checked? i have searched but couldnt really find anything about this.
Thank you.
Lets say i have the situation in the image below.
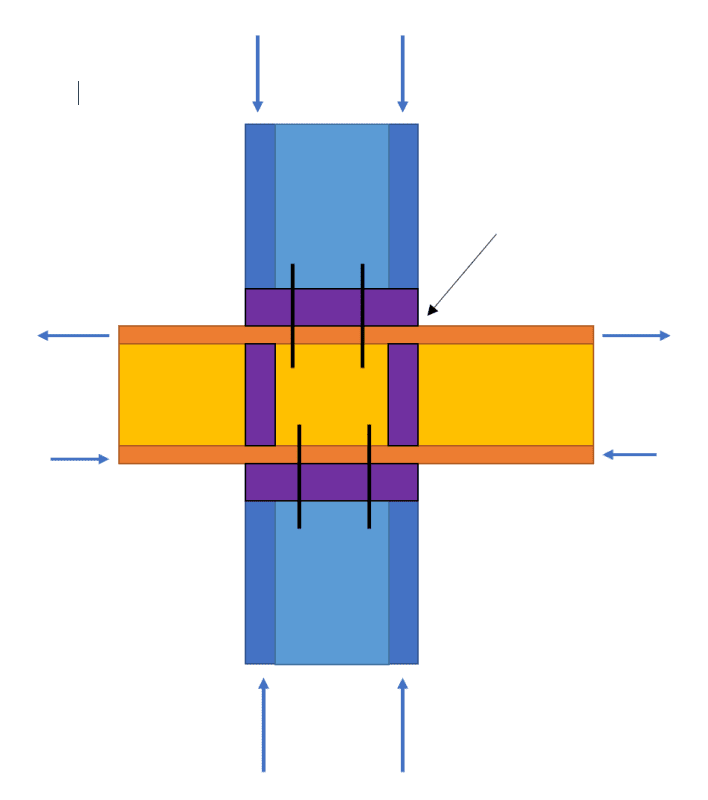
Lets say that the stress in the column is near yielding. The compression force has to go trough the plate, then the flange and then the stiffeners down to the other column.
Wouldnt this mean that the flange under the column is also close to yielding and any bending moment added to the beam would result in failure of the beam. because these stresses need to be combined? Or does this effect not have to be checked? i have searched but couldnt really find anything about this.
Thank you.