hirschaplin
Petroleum
Hello,
Working on the design of a compressor casing in material grade EN-GJS-400-18-LT as per EN 1563:2018. Ultimately I want the compressor casing to fulfill PED, ASME code and API 619 requirements.
The material selection origins from API 619 that suggest that this material may be selected for the compressor casing, see below highlight.
Casing
The minimum recommended temperature is -20 deg C which is inline with the impact values specified in EN 1563:
My questions are the following:
[ol 1]
[li]EN 1563:2018 is suppose to be harmonized with PED 2014/68/EU with conformity since 30/09/2019. And PED is stating the following:
How is this working with the above highlighted minimum impact energy values that are at 10-12 depending on the thickness and therefore less than the required 27 J to my understanding? I know that some pressure codes provide a method to re-calculate impact values based on material thickness, is that relevant here or can someone please explain why values below 27 J are deemed acceptable (through its harmonization) to satisfy PED requirements?
[/li]
[li]In addition to PED and ASME code requirements, there are some specific API 619 requirements for ductile iron castings that need to be fulfilled:
These requirements seems more stringent than the minimum requirements specified in EN 1563 showed above. Is it realistic to think that the material would pass on these API 619 requirements?
[/li]
[li]I would like to use design temperature -29 deg C for the compressor casing. How is that working with the above limitations of -20 deg C? What if the impact test is performed at -29 or -30 deg C instead of -20 deg C? Which are the values to pass? Will the specified material pass at a lower temperature than -20 deg C?
[/li]
[li]My next thinking here was to double certify the material, meaning that the foundry issue a material certificate that states compliance to:
- EN 1563:2018 grade EN-GJS-400-18-LT
- ASTM A395 Grade 60-40-18
Since ASTM A395 Grade 60-40-18 is allowed for -29 deg C as per above yellow highlight in API 619 code.
Then I realize that ASME code and PED has different impact requirements where I understand PED to be the more stringent of the two with higher impact values. Hence perhaps A395 Grade 60-40-18 would pass ASME code and not PED?
Is it possible to dual certify the material to these two different grades and standards as well as fulfilling impact requirements of API 619, PED and ASME code?
[/li]
[li]Which parameters must be fulfilled to claim compliance with NACE MR0103 and NACE MR0175?[/li]
[/ol]
Working on the design of a compressor casing in material grade EN-GJS-400-18-LT as per EN 1563:2018. Ultimately I want the compressor casing to fulfill PED, ASME code and API 619 requirements.
The material selection origins from API 619 that suggest that this material may be selected for the compressor casing, see below highlight.
Casing
Code:
Material Specification Oil-Flooded, Dry-Screw Form °C Min. °C Max. °F Min. °F Max.
Gray iron ASTM A278 class 40 OF Cast – 29 260 – 20 500
Gray iron EN 1561 GJL-250 OF & DS Cast – 10 250 14 482
Gray iron JIS G 5501 FC250 OF Cast – 29 232 – 20 450
Gray iron JIS G 5501 FC300 OF & DS Cast – 29 232 – 20 450
Gray iron JIS G 5501 FC350 OF Cast – 29 232 – 20 450
Ductile iron ASTM A395, grade 60 OF Cast [highlight #FCE94F]– 29[/highlight] 260 – 20 500
Ductile iron EN 1563 GGG 40.3 DS Cast – 20 300 – 4 572
Ductile iron EN 1563 GJS-400-15 OF & DS Cast – 10 250 14 482
[highlight #FCE94F]Ductile iron EN 1563 GJS-400-18-LT OF & DS Cast – 20 300 – 4 572[/highlight]
Steel ASTM A216 grade WCB DS & DS Cast – 29 400 – 20 750
Steel EN 10213 (all parts) GP240 GH OF & DS Cast – 10 300 14 572
Steel EN 10213 (all parts) GS-21Mn5 OF Cast – 46 343 – 51 649
Steel JIS G 5152 SCPL1 OF Cast – 45 350 – 49 662
Steel JIS G 5152 SCPL11 OF & DS Cast – 60 350 – 76 662
Steel JIS G 5152 SCPL21 OF Cast – 75 200 – 103 392
Steel JIS G 5152 SCPL31 OF Cast – 100 200 – 148 392
Steel JIS G 5202 SCW480 OF & DS Cast – 29 399 – 20 750
Steel JIS G 5121 SCS13 DS Cast – 196 350 – 321 662
SS ASTM A351 CF3, CF3M, CF8, CF8M DS Cast – 196 343 – 320 650
SS ASTM A351 grade CF3, CF3M DS Cast – 195 345 – 319 653
SS ASTM A743 grade CA6 - NM DS Cast – 195 345 – 319 653
SS EN 10213 GX3 CrNiMo13-4 DS Cast – 105 300 – 157 572
SS EN 10213 GX5CrNiMoNb19-11- 2 DS Cast – 200 300 – 328 572
SS JIS G 5121 SCS14 DS Cast – 196 350 – 321 662
SS JIS G 5121 SCS5/13Cr-4Ni DS Cast – 196 350 – 321 662
The minimum recommended temperature is -20 deg C which is inline with the impact values specified in EN 1563:
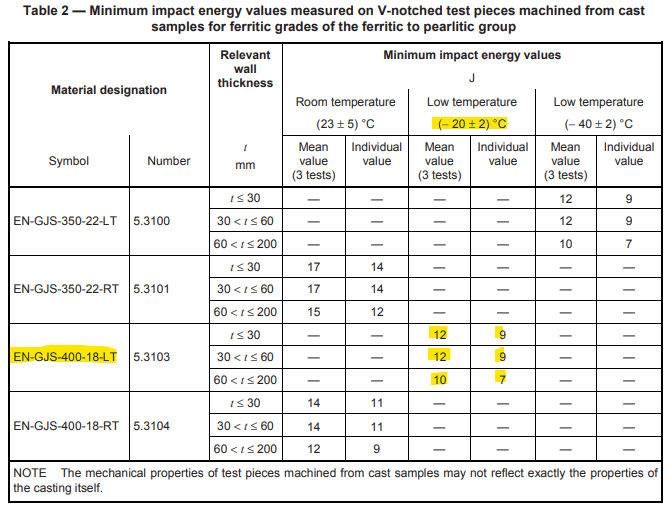
My questions are the following:
[ol 1]
[li]EN 1563:2018 is suppose to be harmonized with PED 2014/68/EU with conformity since 30/09/2019. And PED is stating the following:
PED 2014/68/EU said:7.5. Material characteristics
Unless other values are required in accordance with other criteria that shall be taken into account, a steel is considered as sufficiently ductile to satisfy point 4.1(a) if, in a tensile test carried out by a standard procedure, its elongation after rupture is no less than 14 % and its bending rupture energy measured on an ISO V test-piece is no less than 27 J, at a temperature not greater than 20 °C but not higher than the lowest scheduled operating temperature.
How is this working with the above highlighted minimum impact energy values that are at 10-12 depending on the thickness and therefore less than the required 27 J to my understanding? I know that some pressure codes provide a method to re-calculate impact values based on material thickness, is that relevant here or can someone please explain why values below 27 J are deemed acceptable (through its harmonization) to satisfy PED requirements?
[/li]
[li]In addition to PED and ASME code requirements, there are some specific API 619 requirements for ductile iron castings that need to be fulfilled:
API_619_FIFTH_EDITION_DECEMBER_2010_Para_5.11.2.3.3 said:A minimum of one set (three samples) of Charpy V-notch impact specimens at one-third the thickness
of the test block shall be made from the material adjacent to the tensile specimen on each keel or Y-block. All
three specimens shall have an impact value not less than 11 J (8,1 ft-lbf) and the mean of the three specimens
shall not be less than 14 J (10 ft-lbf) at room temperature.
These requirements seems more stringent than the minimum requirements specified in EN 1563 showed above. Is it realistic to think that the material would pass on these API 619 requirements?
[/li]
[li]I would like to use design temperature -29 deg C for the compressor casing. How is that working with the above limitations of -20 deg C? What if the impact test is performed at -29 or -30 deg C instead of -20 deg C? Which are the values to pass? Will the specified material pass at a lower temperature than -20 deg C?
[/li]
[li]My next thinking here was to double certify the material, meaning that the foundry issue a material certificate that states compliance to:
- EN 1563:2018 grade EN-GJS-400-18-LT
- ASTM A395 Grade 60-40-18
Since ASTM A395 Grade 60-40-18 is allowed for -29 deg C as per above yellow highlight in API 619 code.
Then I realize that ASME code and PED has different impact requirements where I understand PED to be the more stringent of the two with higher impact values. Hence perhaps A395 Grade 60-40-18 would pass ASME code and not PED?
Is it possible to dual certify the material to these two different grades and standards as well as fulfilling impact requirements of API 619, PED and ASME code?
[/li]
[li]Which parameters must be fulfilled to claim compliance with NACE MR0103 and NACE MR0175?[/li]
[/ol]