tmalik3156
Structural
Good day all.
A 32 m long bridge is to be constructed on a rural road over a small river. Sketches of the conceptual design are shown below.
Kindly take a look and advise if this concept looks acceptable. For example, what do you think of using a single row of piles, having no batter, use of a bin-box to retain the soil behind the pile cap?
It's a low budget project, and construction simplicity is preferred.
Do you see any obvious mistakes in this concept design?
ULS vertical load at each corner of the superstructure = 800 kN. ULS longitudinal load at each fixed bearing (due to Breaking force) = 180 kN - generating a deflection at pile cap of 50 mm.
Piles are designed from Geotech skin friction values. Seismic and flood overtopping loads are not required to be considered.
I am not requesting you to do any calculations. But please comment if the concept looks safe and constructible. Any suggestion to improve the design in a cost-effective way is also appreciated.
Thank you
A 32 m long bridge is to be constructed on a rural road over a small river. Sketches of the conceptual design are shown below.
Kindly take a look and advise if this concept looks acceptable. For example, what do you think of using a single row of piles, having no batter, use of a bin-box to retain the soil behind the pile cap?
It's a low budget project, and construction simplicity is preferred.
Do you see any obvious mistakes in this concept design?
ULS vertical load at each corner of the superstructure = 800 kN. ULS longitudinal load at each fixed bearing (due to Breaking force) = 180 kN - generating a deflection at pile cap of 50 mm.
Piles are designed from Geotech skin friction values. Seismic and flood overtopping loads are not required to be considered.
I am not requesting you to do any calculations. But please comment if the concept looks safe and constructible. Any suggestion to improve the design in a cost-effective way is also appreciated.
Thank you
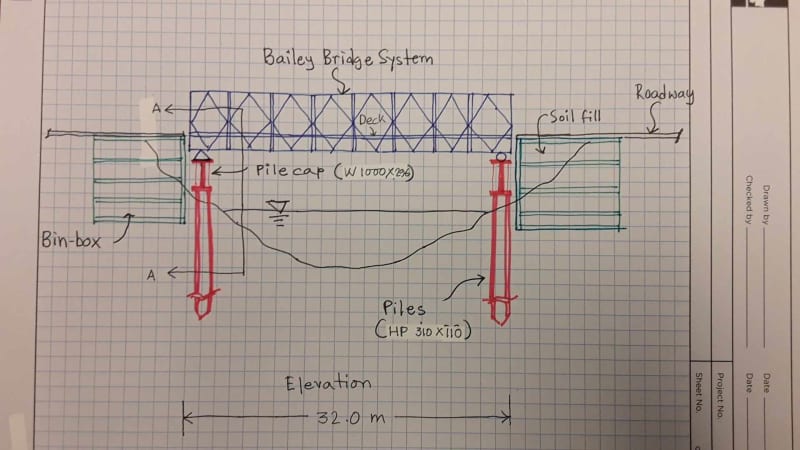
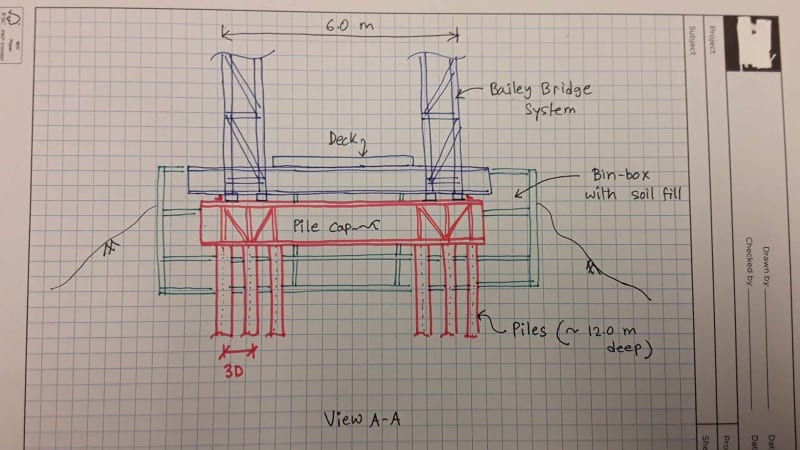