Hi All,
Had a question regarding Column Transitions like the below.
If we have a column over (1000 x 200) and column under (1000 x 200) but rotated and we wanted to check Bearing.
I've been advised to check the bearing of the slab (Top and Bottom of Slab) as this is usually lower in concrete strength.
Questions
1. Is the A1 area correct?
2. What can I take as A2 to increase bearing capacity as this is slightly confusing. And it needs to be geometrically similar to and concentric with A1 as per Section 12.6?
3. Can we use the effective concrete strength from the below in AS3600 (Section 10.8) to increase Bearing capacity in the formula for Section 12.6?
Had a question regarding Column Transitions like the below.
If we have a column over (1000 x 200) and column under (1000 x 200) but rotated and we wanted to check Bearing.
I've been advised to check the bearing of the slab (Top and Bottom of Slab) as this is usually lower in concrete strength.
Questions
1. Is the A1 area correct?
2. What can I take as A2 to increase bearing capacity as this is slightly confusing. And it needs to be geometrically similar to and concentric with A1 as per Section 12.6?
3. Can we use the effective concrete strength from the below in AS3600 (Section 10.8) to increase Bearing capacity in the formula for Section 12.6?
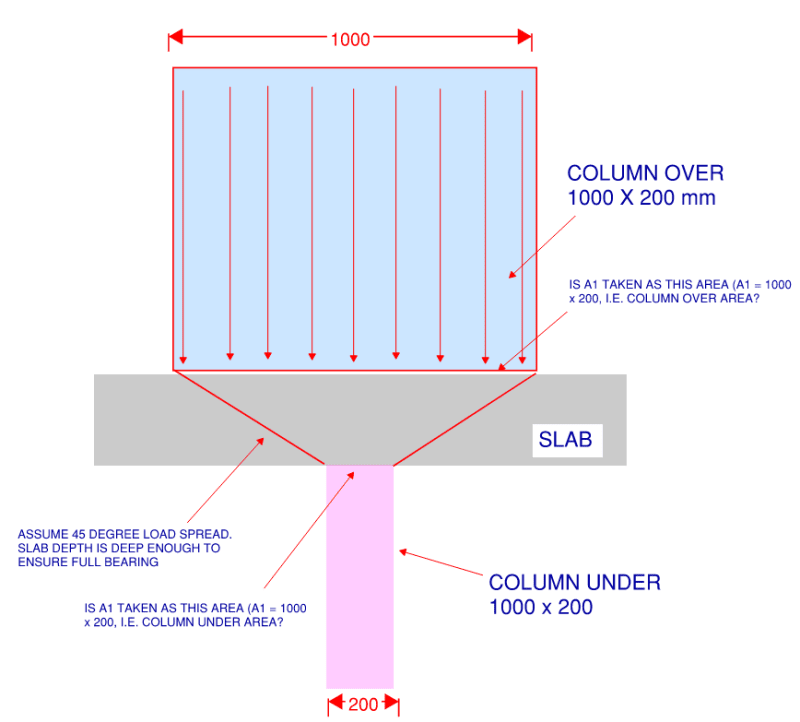
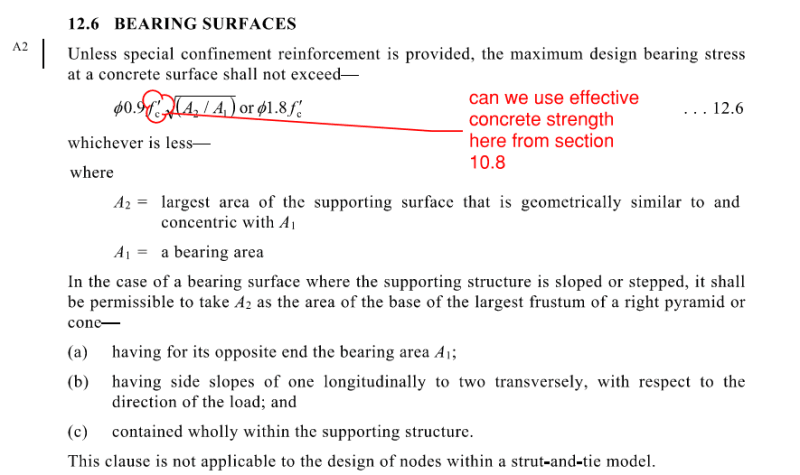
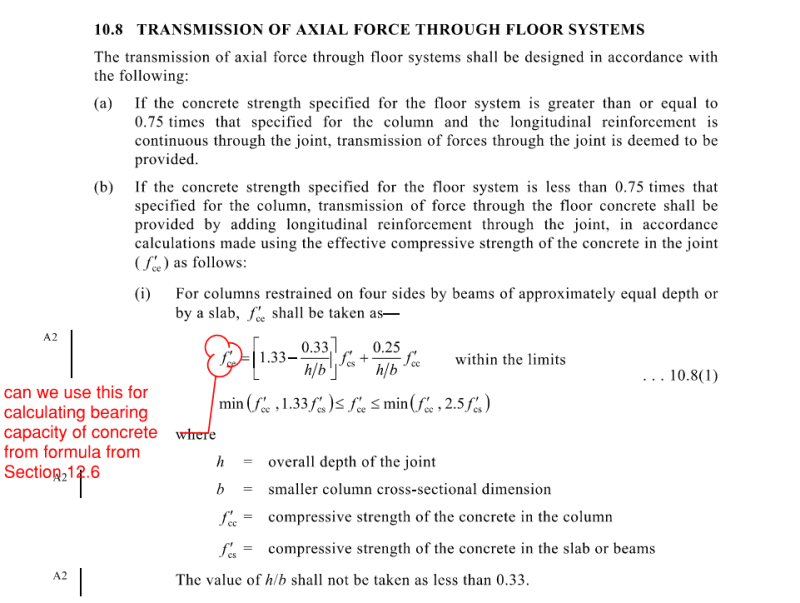